Traditional Craftsmanship Disrupts Digital Fabrication explores the fascinating intersection of time-honored techniques and cutting-edge technology. This dynamic exchange reveals how age-old artistry is being revitalized by digital fabrication, from 3D printing to laser cutting. The evolving landscape presents both challenges and opportunities for artisans, prompting a crucial discussion on the future of craft.
The interplay between traditional craftsmanship and digital fabrication is more than just a technological advancement; it’s a cultural dialogue. This discussion delves into the historical context of craftsmanship, highlighting its evolution and economic significance. It also examines the core principles of digital fabrication, outlining its advantages and disadvantages, and showcasing how these methods can potentially enhance traditional techniques.
Historical Context of Craftsmanship
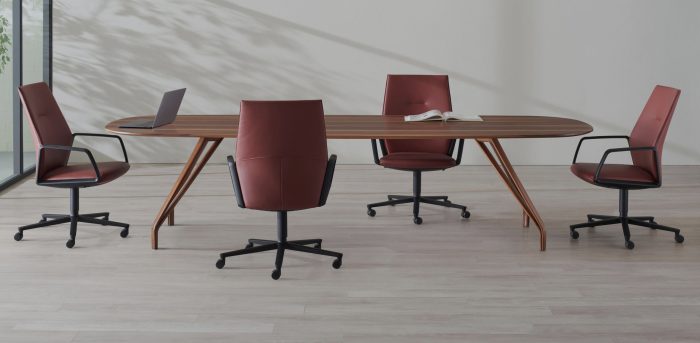
Source: architizer.com
Traditional craftsmanship, a cornerstone of human ingenuity and artistry, has a rich history deeply intertwined with societal development. From the creation of intricate tools to the construction of magnificent structures, craftsmanship has always been a driving force in shaping cultures and economies. This enduring tradition, passed down through generations, represents a profound connection between human creativity and the material world.
Early forms of craftsmanship were intrinsically linked to survival, evolving alongside the development of tools and techniques.The practice of craftsmanship, while often associated with a specific era, has continuously adapted and evolved to meet the demands of society. The tools and techniques employed in craftsmanship have changed dramatically over time, mirroring advancements in materials science and engineering. This evolution highlights the dynamic nature of craftsmanship and its capacity to adapt to changing circumstances.
Key Periods and Influential Figures
Craftsmanship has flourished across various periods, with distinct styles and techniques emerging. The ancient Egyptians, renowned for their monumental architecture and intricate artwork, exemplify early mastery of construction and decorative arts. The Greeks and Romans further developed these traditions, introducing innovative architectural styles and sophisticated metalworking techniques. The medieval period witnessed the rise of guilds, which fostered skilled artisans and established quality standards.
The Renaissance saw a resurgence of classical ideals, leading to a flourishing of artistic expression and intricate craftsmanship. The Industrial Revolution marked a significant shift, introducing new materials and manufacturing processes that began to reshape the landscape of craftsmanship.
Evolution of Tools and Techniques
The development of tools and techniques in traditional craftsmanship is closely tied to the materials available and the prevailing societal needs. Early tools, often fashioned from stone, wood, or bone, were rudimentary but effective. The discovery of metalworking techniques revolutionized the field, allowing for the creation of more sophisticated tools and artistic objects. The evolution of woodworking techniques, from simple hand tools to complex power tools, showcases the ingenuity of craftsmen.
The introduction of the printing press fundamentally changed the way information was disseminated, altering the social and economic landscape of craftsmanship.
Comparison with Early Industrialization
Traditional craftsmanship, deeply rooted in individual skill and meticulous attention to detail, contrasted sharply with the early forms of industrialization. Industrialization, while fostering mass production and efficiency, often prioritized speed and standardization over the artistry and unique character of handcrafted items. The transition from hand-crafted goods to machine-made products brought about both economic advantages and potential losses in artistic expression and personal touch.
This shift in production methods led to both significant economic changes and the eventual evolution of specialized labor roles within society.
Social and Economic Significance
Throughout history, traditional craftsmanship has held significant social and economic value. It provided employment opportunities, fostered communities, and transmitted cultural knowledge across generations. The craftsmanship of a region often reflected its unique identity and traditions, creating a sense of place and shared heritage. The social significance of traditional craftsmanship can be seen in the intricate details of religious objects or the artistry of everyday items.
Artisans were often highly respected members of society, possessing specialized knowledge and skills valued for their utility and aesthetic appeal.
Strengths and Weaknesses of Traditional Craftsmanship Methods
Craftsmanship Method | Strengths | Weaknesses |
---|---|---|
Hand-carved Woodworking | High degree of customization, unique aesthetic appeal, deep personal connection with the product, fostering meticulous detail | Time-consuming, limited production scale, often requiring specialized skills |
Pottery | Flexibility in form and design, rich sensory experience, strong connection to the natural materials, artistic freedom | Potentially fragile products, time-intensive process, variable quality control, reliance on natural materials |
Blacksmithing | Durable, strong, and long-lasting products, high level of craftsmanship, unique artistry, connection to metal forging techniques | Time-consuming, high skill requirement, limited production capacity, susceptibility to material defects |
Weaving | Varied textures and patterns, connection to natural fibers, creation of unique textiles, aesthetic appeal, rich cultural significance | Time-consuming, reliance on natural fibers, potentially limited production scale, high skill requirement |
Defining Traditional Craftsmanship
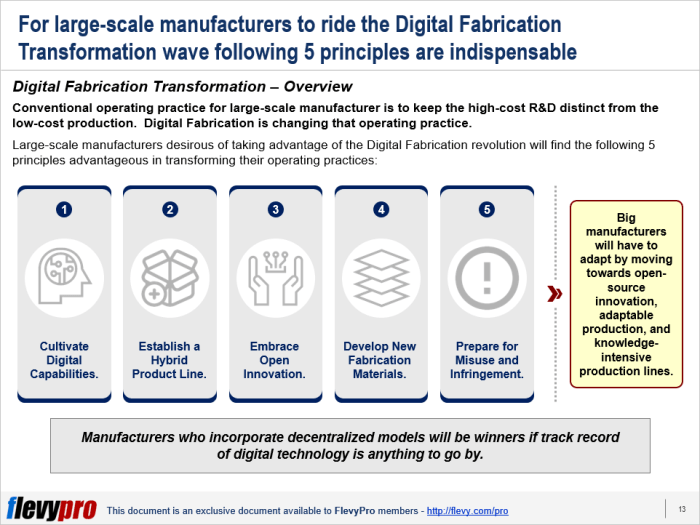
Source: flevy.com
Traditional craftsmanship represents a profound departure from the standardized, mass-produced goods that dominate modern markets. This approach emphasizes the unique artistry and meticulous skill of the individual artisan, resulting in pieces that are often imbued with cultural significance and aesthetic value. The very process of creation, from initial design to final execution, carries a story that is distinct from the impersonal nature of industrial production.Traditional craftsmanship is characterized by a complex interplay of skill, knowledge, and experience, often passed down through generations.
This transmission of techniques and aesthetic sensibilities creates a continuity of cultural heritage. In contrast to the standardized products of modern manufacturing, traditional crafts often display a certain degree of variation and individuality, reflecting the unique hand of the artisan.
Characteristics of Traditional Craftsmanship
Traditional craftsmanship differs significantly from mass-produced goods due to several key characteristics. These characteristics are deeply rooted in the values and practices of specific cultures and regions. These characteristics are the result of a deep-seated understanding of materials, techniques, and aesthetic principles, often honed over many years of practice.
- Emphasis on Skill and Knowledge: Traditional craftsmanship relies heavily on the expertise of the artisan. Deep knowledge of materials, tools, and techniques is critical, often acquired through years of apprenticeship and practice. This contrasts sharply with the replaceable nature of labor in mass production.
- Hand-Made Nature: Unlike mass-produced goods, traditional crafts are made entirely by hand. This inherent human touch gives each piece a unique identity and character that cannot be replicated by machines.
- Cultural Significance: Many traditional crafts are deeply intertwined with the cultural heritage of the region or community. They often embody symbolic meanings and historical narratives, reflecting the values and beliefs of the people who created them.
- Focus on Quality: Craftsmanship prioritizes the quality of materials and the precision of execution. Artisans are highly attuned to detail and strive for excellence in their work. This emphasis on quality contrasts with the focus on speed and cost-effectiveness in mass production.
Examples of Traditional Crafts
Traditional crafts are diverse and widely distributed across the globe. Each culture has developed its own distinctive crafts, reflecting the local environment, materials, and artistic sensibilities. These crafts often play a significant role in the daily lives of communities.
- Japanese Pottery (e.g., Kintsugi): This ancient craft emphasizes the beauty of imperfections, skillfully repairing broken pottery with gold or lacquer. This philosophy highlights the cultural value placed on mending and restoration.
- African Wood Carving: These intricate sculptures, often depicting animals, figures, or abstract forms, are central to many African cultures. They are imbued with cultural symbolism and spiritual significance.
- Textiles from India (e.g., Ikat, Kantha): The vibrant and intricate patterns of Indian textiles, such as Ikat and Kantha, are a testament to the artistry and skill of generations of weavers. These techniques often involve complex dyeing and weaving processes.
- Mexican Talavera Pottery: This brightly colored ceramic ware is known for its elaborate designs and intricate glazing techniques. The colorful patterns often reflect local history and culture.
The Role of Skill, Knowledge, and Experience
The expertise of the artisan is paramount in traditional craftsmanship. The process often involves years of dedicated training and practice, ensuring the creation of high-quality pieces.
- Apprenticeships: A significant aspect of traditional craftsmanship is the apprenticeship system. Learners work alongside experienced masters, acquiring practical skills and theoretical knowledge over time.
- Passing Down Knowledge: The knowledge and techniques of traditional craftsmanship are often passed down through generations. This continuous transmission ensures the preservation of cultural heritage.
- Development of Individual Style: Over time, artisans develop a unique style based on their acquired knowledge and experience. This personalized touch differentiates their work from others, adding to its value.
Aesthetic Qualities of Traditional Crafts
Traditional crafts often possess distinctive aesthetic qualities that distinguish them from mass-produced items. These qualities reflect the values and cultural context in which they were created.
- Intricate Detail: Traditional crafts often feature intricate patterns, designs, and embellishments. The attention to detail highlights the dedication and skill of the artisan.
- Unique Design: Traditional crafts are typically unique and not easily replicated. This individuality arises from the artisan’s personal style and the use of specific techniques and materials.
- Cultural Expression: Many traditional crafts reflect the cultural values and beliefs of the community. These pieces often serve as a tangible expression of a community’s history and identity.
Table of Diverse Traditional Crafts, Traditional Craftsmanship Disrupts Digital Fabrication
Culture/Region | Craft | Key Characteristics |
---|---|---|
Japan | Kintsugi Pottery | Repairing broken pottery with gold or lacquer; emphasizing beauty of imperfections |
Africa | Wood Carving | Intricate sculptures depicting animals, figures, or abstract forms; embodying cultural symbolism |
India | Ikat Textiles | Vibrant and intricate patterns created through dyeing and weaving; showcasing artistry and skill |
Mexico | Talavera Pottery | Elaborate designs and intricate glazing techniques; colorful patterns reflecting local history |
Exploring Digital Fabrication
Digital fabrication, encompassing technologies like 3D printing and CNC machining, represents a significant departure from traditional methods. This approach leverages digital design and computational processes to create physical objects, often with unprecedented levels of precision and customization. This shift is fundamentally altering the landscape of manufacturing, design, and even artistic expression.
Core Principles of Digital Fabrication
Digital fabrication hinges on the ability to translate digital designs into physical realities. This process typically involves computer-aided design (CAD) software to create detailed 3D models. These models are then processed through specialized software and hardware, which translates the digital instructions into instructions for physical machines. This digital intermediary allows for greater control over design parameters and production processes.
Processes in Digital Fabrication
The core processes involved in digital fabrication are iterative and rely on digital tools. First, a 3D model is created using CAD software. Next, the model is sliced into layers, a process critical for additive manufacturing techniques like 3D printing. These layers are then meticulously printed, one after another, to construct the final object. Alternatively, in subtractive manufacturing (e.g., CNC machining), the digital model dictates the precise removal of material to achieve the desired shape.
This intricate interplay between digital design and physical execution is at the heart of digital fabrication.
Revolutionizing Design and Production
Digital fabrication technologies, particularly 3D printing, are revolutionizing design and production in various sectors. Designers can explore complex geometries and intricate details previously impossible to realize with traditional methods. The ability to rapidly prototype and iterate designs leads to faster development cycles and greater efficiency. The potential for personalized and customized products is also a major advantage.
Advantages of Digital Fabrication
- Customization and Personalization: Digital fabrication allows for the creation of highly customized products, catering to individual needs and preferences. For example, a consumer can design a unique piece of jewelry or a specialized tool that precisely meets their requirements.
- Rapid Prototyping and Iteration: The ability to quickly produce prototypes enables designers and engineers to iterate on designs and identify improvements rapidly. This leads to faster product development cycles and cost savings.
- Reduced Material Waste: Digital fabrication methods can often utilize material more efficiently than traditional methods. 3D printing, for example, can deposit material precisely where needed, minimizing waste.
- Design Complexity: Complex shapes and intricate geometries are achievable with digital fabrication techniques, which were previously impractical or impossible to create using traditional methods.
Disadvantages of Digital Fabrication
- Cost of Equipment: High-quality 3D printers and CNC machines can be expensive to acquire and maintain, posing a significant barrier to entry for smaller businesses.
- Material Limitations: The range of materials compatible with digital fabrication technologies is not as broad as traditional methods. The choice of materials often affects the strength, durability, and aesthetics of the final product.
- Potential for Errors: Digital models can contain errors that translate into defects in the final product, requiring careful attention to detail during the design and fabrication process.
- Scalability Challenges: While digital fabrication is excellent for small-scale production, scaling up to mass production can sometimes present challenges.
Examples of Modern Products and Designs
Digital fabrication is now widely used in diverse industries. From intricate medical implants to customized architectural components, the application of digital fabrication is expanding rapidly. Specialized prosthetics, personalized dental crowns, and complex architectural structures are now routinely fabricated using these methods.
Comparison of Production Timelines and Costs
Feature | Traditional Fabrication | Digital Fabrication |
---|---|---|
Production Time | Generally longer, dependent on complexity and skill level | Potentially faster, especially for prototyping and small-batch production |
Material Cost | May be higher depending on material availability and waste | Potentially lower with optimized material use |
Labor Cost | Higher labor costs for skilled craftspeople | Lower labor costs for operation of machines, but potentially higher for design and software expertise |
Setup Time | Longer setup time to prepare tools and materials | Shorter setup time for digital files and machine calibration |
Customization | Limited customization, often batch-based | High degree of customization, adaptable to individual requirements |
The Intersection of Craftsmanship and Digital Fabrication: Traditional Craftsmanship Disrupts Digital Fabrication
Traditional craftsmanship, deeply rooted in centuries of practice and skill, often faces challenges in the modern world. Digital fabrication techniques offer a compelling avenue for innovation and revitalization. By exploring the intersection of these two approaches, we can unlock new possibilities for creative expression, efficiency, and accessibility in the world of craft.Digital fabrication tools, like 3D printing and CNC machining, can serve as powerful allies to traditional artisans.
They can enhance existing techniques by providing precise measurements, repeatable actions, and the ability to create complex forms impossible to achieve by hand alone. Conversely, traditional craftsmanship brings a human touch and aesthetic sensitivity that digital tools often lack. This synergy between the two approaches promises to unlock a new era of creative potential.
Complementary Techniques
Traditional crafts often rely on meticulous handwork, requiring considerable time and skill. Digital fabrication techniques, on the other hand, excel at rapid prototyping and the creation of intricate details. These techniques can complement each other. For example, a potter might use a digital scanner to precisely capture the form of a sculpted clay vessel. This digital model can then be used to create a mold for casting, significantly increasing production efficiency while maintaining the original artistic intent.
Enhancing Traditional Techniques
Digital fabrication tools can enhance traditional craftsmanship in numerous ways. For example, a woodcarver might use a 3D model to design intricate patterns and then use a CNC router to precisely carve the design into a piece of wood. This approach ensures the intricate details are perfectly executed while conserving the carver’s time and effort. Another example includes using a 3D printer to create complex patterns for embroidery or quilting, allowing for the creation of highly intricate and detailed designs.
Artistic Expression
The artistic expression achievable through traditional and digital fabrication methods differ significantly. Traditional methods often involve a unique interplay between the artist’s skill and the material’s properties. The variations in the material, the imperfections of hand-crafted elements, and the individual artist’s touch contribute to the piece’s unique character. Digital fabrication, while capable of intricate details, often relies on the pre-defined digital model.
The artist’s control over the process is indirect, influencing the outcome through the digital design. The resulting piece may have a more uniform and controlled appearance.
Impact on Availability and Accessibility
Digital fabrication can democratize traditional crafts by making them more accessible to a wider range of individuals. For example, 3D printing allows individuals to create personalized and customized objects based on traditional designs. This accessibility fosters creativity and innovation while enabling the preservation of traditional knowledge. Furthermore, digital tools can make intricate designs, once reserved for skilled artisans, available to a wider range of enthusiasts and students, enabling the dissemination and perpetuation of traditional crafts.
Reproducing, Modifying, and Enhancing Traditional Designs
Traditional Design | Digital Fabrication Application | Result |
---|---|---|
A complex, intricate woven tapestry | 3D scanning and 3D printing | High-fidelity replica of the tapestry, allowing for easy reproduction or even customization of colors and patterns. |
A carved wooden mask | 3D scanning and CNC milling | A precise replica of the mask, enabling the creation of multiple identical masks, or the modification of existing designs to create variations. |
A traditional pottery design | Digital modeling and 3D printing | Allows for the creation of intricate patterns and designs not possible with traditional methods, or the replication of a specific design with high precision. |
A traditional metalwork design | Digital modeling and CNC machining | Enables intricate and complex metalwork designs with precision, potentially leading to a more intricate and detailed final product, or the replication of a design with greater efficiency. |
Digital fabrication techniques offer a means to reproduce, modify, and even enhance traditional designs, potentially revitalizing traditional crafts and fostering innovation.
Economic and Social Implications
The convergence of traditional craftsmanship and digital fabrication presents a complex interplay of economic and social factors. The emergence of digital tools challenges established market dynamics, impacting employment prospects and cultural preservation. Understanding these intricate relationships is crucial for navigating the future of both sectors.The market for traditional crafts is undergoing a transformation, as digital fabrication offers alternatives for producing goods.
While this can lead to increased competition, it also presents opportunities for innovation and adaptation. Artisans who successfully integrate digital tools into their practices can expand their market reach and potentially enhance the perceived value of their work. Conversely, those resistant to change may face challenges in maintaining their market share.
Impact on the Market for Traditional Crafts
Digital fabrication techniques, like 3D printing and CNC machining, are capable of replicating certain handcrafted items. This creates a direct competition in the market, potentially reducing demand for uniquely crafted, one-of-a-kind pieces. However, digital fabrication also opens new avenues for traditional craft. Artisans can use these tools to enhance their designs, explore new possibilities, and create intricate patterns that might be challenging to execute by hand.
This can lead to the development of new and unique products, expanding the market for traditional craft and creating a fusion of traditional and modern aesthetics.
Potential Impact on Employment
The introduction of digital fabrication will undoubtedly reshape employment in both traditional and digital fabrication sectors. The rise of automated production might lead to job displacement in some traditional craft sectors, but it also necessitates a shift in skillsets and the emergence of new roles. Artisans will need to adapt to the new technologies, learning to use digital fabrication tools alongside their traditional techniques.
In the digital fabrication sector, there will be a demand for skilled technicians and designers to operate and program these machines. The long-term impact on employment depends heavily on how effectively artisans and digital fabricators adapt to the changing landscape.
Role of Traditional Craftsmanship in Cultural Preservation and Identity
Traditional craftsmanship plays a vital role in preserving cultural heritage and identity. Handcrafted objects often hold significant cultural and historical value, reflecting the traditions, beliefs, and stories of a community. They serve as tangible links to the past, conveying cultural narratives and fostering a sense of belonging. The preservation of these skills and traditions is crucial for maintaining cultural identity in a rapidly changing world.
Examples of Initiatives Promoting Fusion
Several initiatives are exploring the fusion of traditional craftsmanship and digital fabrication. One example involves incorporating 3D-printed components into handcrafted furniture, enhancing its functionality and design. Another approach involves using digital design tools to create intricate patterns and motifs for traditional textile crafts, enabling artisans to produce more elaborate and visually striking pieces. These efforts highlight the potential for synergistic growth and creative exploration within these fields.
Potential Economic Benefits and Challenges for Artisans
Aspect | Potential Benefits | Potential Challenges |
---|---|---|
Increased Efficiency | Faster production times, reduced material waste, improved cost-effectiveness. | Dependence on technology, need for training, potential for quality issues. |
Expanded Market Reach | Access to global markets, wider customer base, potential for higher revenue. | Increased competition from mass-produced items, maintaining unique selling propositions. |
New Design Possibilities | Integration of digital designs with traditional techniques, exploration of innovative styles. | Learning curve for new software and tools, maintaining control over the design process. |
Improved Quality Control | Precision in design and execution, consistent quality across multiple pieces. | Potential for technical issues and errors during digital fabrication processes. |
“The fusion of traditional craftsmanship and digital fabrication is not about replacing one with the other, but about leveraging the strengths of both to create new possibilities.”
The Future of Craft
The intersection of traditional craftsmanship and digital fabrication presents a compelling vision for the future of craft. This evolving landscape offers opportunities for innovation, preservation, and economic growth within the artistic community. By integrating digital tools into established practices, artisans can enhance their capabilities, explore new creative avenues, and reach wider audiences.
Potential of Integrating Digital Fabrication
Digital fabrication technologies, such as 3D printing, laser cutting, and CNC milling, offer a powerful means of enhancing traditional craft practices. These technologies allow for intricate designs, precise measurements, and rapid prototyping, enabling artisans to experiment with new forms and functionalities. The precision and customization afforded by digital fabrication can transform the design and production process, enabling a higher level of artistic expression.
Modernizing Traditional Crafts
Numerous examples showcase the modernization of traditional crafts through the integration of digital fabrication. Pottery artisans are leveraging 3D printing to create complex forms and intricate designs, pushing the boundaries of traditional methods. Similarly, woodworkers are using CNC routers to craft intricate furniture and decorative objects, adding speed and accuracy to their production. Jewelry designers are exploring 3D printing to create unique and personalized pieces, expanding their creative options and reaching a broader customer base.
This fusion of old and new techniques results in innovative creations that maintain the essence of traditional craftsmanship while embracing the possibilities of digital fabrication.
Emerging Trends and Innovations
Several trends are shaping the intersection of traditional craftsmanship and digital fabrication. Parametric design software is enabling artists to create highly customized and intricate designs for their products. The use of open-source software and digital fabrication tools is promoting accessibility and collaboration within the craft community. Moreover, the integration of augmented reality (AR) and virtual reality (VR) technologies is allowing for the visualization and exploration of designs before physical production.
Projected Future Scenarios
Scenario | Description |
---|---|
Hybrid Production | Craftspeople use digital fabrication to create complex components or patterns, then hand-finish and assemble them, combining precision with artistic touch. This approach allows for both the speed and complexity of digital fabrication and the artistic expression of traditional techniques. |
Personalized Customization | Digital fabrication enables the creation of highly personalized products, tailored to individual customer specifications. This approach blends traditional craftsmanship with the ability to meet the unique needs and desires of each customer. |
Collaborative Design | Online platforms and digital tools facilitate collaboration between craftspeople and designers. This allows for the sharing of ideas, the creation of innovative designs, and the expansion of production capabilities beyond the individual artisan’s limitations. |
Preservation of Traditional Skills | Digital fabrication assists in the preservation and transmission of traditional techniques. By documenting and replicating intricate processes, the knowledge and skills of experienced craftspeople can be shared and passed down to future generations. |
Challenges and Opportunities for Artisans
The integration of digital fabrication into traditional craft practices presents both challenges and opportunities for artisans. The initial investment in digital tools and software can be a significant barrier. However, the potential for increased efficiency, design flexibility, and market reach offers considerable benefits. Furthermore, the need for acquiring new skills in digital fabrication may require a period of adaptation and training.
The potential to create new markets, offer personalized designs, and access global markets is substantial.
Last Recap
In conclusion, the convergence of traditional craftsmanship and digital fabrication presents a compelling narrative of innovation and adaptation. While the future of craft is undeniably evolving, the fundamental values of skill, creativity, and cultural preservation remain central. This fusion promises exciting possibilities for artisans and enthusiasts alike, challenging us to contemplate the enduring power of human ingenuity in shaping the world around us.
Quick FAQs
What are some examples of initiatives promoting the fusion of traditional craftsmanship and digital fabrication?
Numerous initiatives exist, ranging from workshops teaching artisans how to use digital fabrication tools to collaborations between traditional craftspeople and designers. These often involve exploring new possibilities for incorporating digital techniques into traditional methods, creating unique hybrid pieces.
How might digital fabrication impact the market for traditional crafts?
Digital fabrication can both enhance and potentially challenge the market for traditional crafts. On one hand, it can broaden the reach and accessibility of these crafts through reproduction and replication. On the other hand, it might shift the demand dynamics, prompting some consumers to favor readily accessible digitally fabricated alternatives over handcrafted items.
What are the potential economic challenges for artisans adapting to digital fabrication?
Artisans may face challenges in acquiring the necessary digital fabrication skills and tools. There’s also the question of adapting business models and marketing strategies to compete in a market increasingly influenced by digital fabrication. However, the potential economic benefits, such as increased production efficiency and new market opportunities, are also significant.