Revolutionary 3D Printing Techniques Transform Furniture Manufacturing Efficiency is revolutionizing the furniture industry. Traditional methods, often slow and costly, face limitations in design flexibility and material utilization. 3D printing offers a dynamic alternative, enabling intricate designs and personalized furniture pieces while potentially reducing production time and waste. This innovative approach is transforming the manufacturing landscape, offering unprecedented possibilities for both efficiency and aesthetic expression in the creation of furniture.
This document delves into the exciting world of 3D printing in furniture manufacturing, exploring the diverse technologies, materials, and design possibilities. We will examine the impact on manufacturing efficiency, design freedom, and sustainability. Expect a comprehensive overview, addressing the challenges and future trends in this emerging field.
Introduction to Revolutionary 3D Printing in Furniture Manufacturing
Traditional furniture manufacturing often relies on intricate processes involving wood carving, machining, and assembly. These methods, while yielding aesthetically pleasing pieces, frequently face limitations in terms of design complexity, material utilization, and production efficiency. The industry is ripe for innovation, and 3D printing is poised to disrupt the status quo, offering a paradigm shift in how furniture is designed and produced.The limitations of traditional furniture manufacturing methods are multifaceted.
Standardized designs often restrict creativity, while intricate designs can be challenging and time-consuming to produce. Material waste is common, and manufacturing processes can be energy-intensive. These challenges often result in higher production costs and longer lead times. The emergence of 3D printing technology offers a compelling alternative, allowing for the creation of complex, customized designs with unprecedented precision and efficiency.
Overview of Traditional Furniture Manufacturing Methods
Traditional furniture manufacturing commonly involves several steps, starting with material selection. This can range from solid wood to composite materials. Subsequent processes, including cutting, shaping, and assembly, can be labor-intensive and prone to errors. Often, these methods require specialized tools and skilled labor, adding to the overall cost. The standardization of designs in many cases limits customization options, which sometimes fails to meet the specific needs of consumers.
Limitations of Traditional Furniture Manufacturing Methods
Traditional furniture manufacturing methods often struggle with the production of intricate designs. Complex geometries are challenging to achieve with traditional techniques, and often require extensive labor and time. The use of raw materials can also be inefficient, leading to substantial waste. The manufacturing processes themselves can be energy-intensive, contributing to environmental concerns. Further, customization is often restricted to a limited degree.
Emergence of 3D Printing Technology in Manufacturing
D printing, or additive manufacturing, has rapidly evolved, enabling the creation of complex three-dimensional objects from digital designs. This technology is particularly well-suited for furniture production, as it allows for the creation of intricate shapes and customized designs with reduced material waste. The ability to rapidly prototype and iterate on designs significantly accelerates the design-to-production cycle.
Application of 3D Printing to Furniture Design
D printing is revolutionizing furniture design by allowing designers to explore a broader range of aesthetics and functionalities. From innovative chair designs to custom-fitted cabinetry, the technology empowers the creation of unique pieces that cater to specific needs and preferences. The customization options for furniture design are practically limitless, from the intricate patterns to the material choices. This is enabling a more personalized and expressive approach to furniture creation.
Comparison of Traditional and 3D Printing Methods for Furniture Production
Feature | Traditional Manufacturing | 3D Printing |
---|---|---|
Design Complexity | Limited by tooling and techniques | Highly complex designs are possible |
Material Utilization | Potentially high material waste | Reduced material waste, optimized use |
Customization | Limited to pre-defined options | Highly customizable, personalized designs |
Production Time | Often lengthy | Potentially faster prototyping and production |
Cost | Can be high due to labor and tooling | Potential for lower costs in mass production |
Types of 3D Printing Technologies Used in Furniture Production
Various 3D printing technologies are rapidly emerging as powerful tools in the furniture manufacturing process. These methods offer unique advantages in terms of design flexibility, customization, and material utilization. This section explores the different types of 3D printing employed in furniture production, highlighting their strengths and weaknesses, and illustrating their potential applications.Different 3D printing techniques excel at producing different furniture components, catering to diverse design needs and material properties.
Choosing the appropriate technique is critical for achieving desired aesthetic qualities, structural integrity, and manufacturing efficiency.
Fused Deposition Modeling (FDM)
FDM, a widely used additive manufacturing technique, is particularly well-suited for creating intricate designs in thermoplastic materials. The process involves extruding molten plastic through a nozzle to build layers. This approach is cost-effective and allows for the production of complex shapes, but its resolution and structural strength are often limited compared to other techniques.
Stereolithography (SLA)
SLA uses a laser to cure liquid resin layer by layer. This technique yields high-resolution prints with smooth surfaces and detailed features. The material compatibility is primarily focused on resins, offering a variety of colors and finishes, but the process can be more expensive than FDM and is less versatile for complex shapes.
Selective Laser Sintering (SLS)
SLS utilizes a high-powered laser to selectively sinter powdered materials, enabling the creation of strong and durable parts. This process allows for the use of a wide range of materials, including polymers, metals, and composites, providing significant flexibility in material selection for furniture components. However, the process typically requires specialized equipment and expertise.
Material Jetting (MJ)
Material jetting employs inkjet-like technology to precisely deposit material layer by layer. This technique is suitable for intricate designs and complex geometries. MJ is particularly well-suited for intricate decorative elements and functional components within furniture. While it offers good accuracy and detail, the material selection might be more limited compared to SLS.
Direct Metal Laser Sintering (DMLS), Revolutionary 3D Printing Techniques Transform Furniture Manufacturing Efficiency
DMLS is a specialized additive manufacturing process that uses a laser to sinter metallic powders. This technique allows for the creation of highly complex and durable metal parts, offering significant potential for the production of strong and aesthetically pleasing furniture components. The cost and specialized equipment requirements can be a major factor for wider adoption.
Comparison of 3D Printing Methods for Furniture Components
Printing Method | Material Compatibility | Typical Furniture Applications | Strengths | Weaknesses |
---|---|---|---|---|
FDM | Thermoplastics (ABS, PLA, PETG) | Prototypes, decorative accents, simple furniture parts | Cost-effective, versatile designs, readily available materials | Lower resolution, limited strength, surface imperfections |
SLA | Resins | High-detail decorative components, intricate shapes | High resolution, smooth surfaces, detailed features | Limited material choices, higher cost, resin disposal |
SLS | Polymers, metals, composites | Strong structural elements, functional components, prototypes | High strength, wide material range, intricate geometries | High cost, specialized equipment, potential for warping |
MJ | Resins, ceramics | Intricate decorative patterns, detailed functional parts | High precision, complex geometries, suitable for customization | Limited material options, potential for clogging |
DMLS | Metals | Structural components, high-strength parts | High strength, durable parts, intricate designs | High cost, specialized equipment, limited material choices |
Impact on Furniture Design and Aesthetics
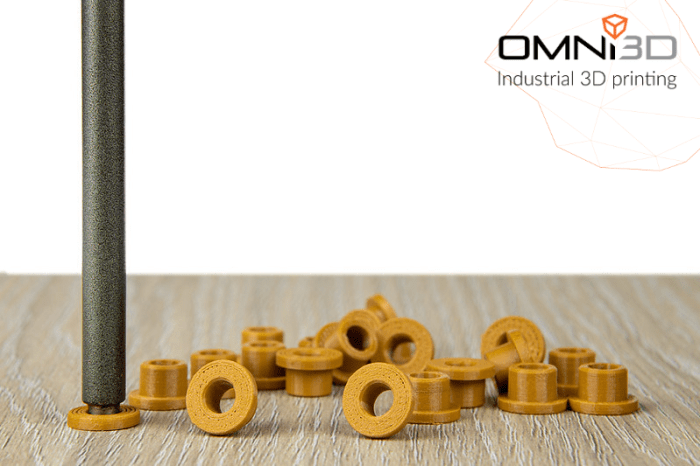
Source: omni3d.com
D printing’s impact on furniture manufacturing extends beyond efficiency; it profoundly alters design possibilities and aesthetic expression. The technology empowers designers with unprecedented freedom to explore intricate shapes, complex geometries, and customized features, leading to a wave of innovative and visually striking furniture pieces.The traditional constraints of woodworking and manufacturing are effectively dismantled by 3D printing, opening a new realm of design potential.
This allows for the creation of highly detailed and personalized furniture that was previously unimaginable.
Design Freedom and Complex Geometries
D printing liberates designers from the limitations of traditional manufacturing methods. The ability to directly translate digital designs into physical objects allows for complex geometries and intricate details that would be impractical or impossible to achieve with conventional methods. This translates into furniture designs that are not only visually appealing but also highly functional.
Unique and Complex Designs
Examples of unique and complex designs achievable with 3D printing abound. Imagine a chair with a flowing, organic shape, impossible to create with traditional joinery techniques. Or a table with a sculpted base that seamlessly integrates with a layered tabletop, exhibiting intricate patterns. These designs are now readily attainable through the precise control offered by 3D printing.
Influence on Furniture Aesthetics
D printing significantly impacts furniture aesthetics by allowing for intricate textures and finishes not possible with traditional methods. The material properties of the 3D printed component can be exploited to create interesting surfaces and patterns, leading to a wide range of visual possibilities. This empowers designers to experiment with diverse materials and finishes, leading to a new aesthetic vocabulary in furniture design.
Customized Furniture Designs
D printing is particularly well-suited for customized furniture designs. A customer can have a unique piece of furniture designed and manufactured to their precise specifications. This customization extends beyond simple dimensions to encompass unique shapes, finishes, and materials. The ability to tailor furniture to individual preferences is a key advantage of 3D printing in the furniture industry.
Table of 3D-Printed Furniture Designs
Design | Unique Features | Material | Aesthetic Impact |
---|---|---|---|
Organic Chair | Fluid, flowing form; integrated armrests; minimal visible joints | PLA (polylactic acid) | Modern, minimalist; organic shapes |
Sculptural Table | Intricate base design; layered tabletop with embedded patterns; custom finish | ABS (acrylonitrile butadiene styrene) | Contemporary; strong visual impact; customizable details |
Modular Shelving System | Variable heights and widths; customized storage compartments; curved edges | Carbon Fiber reinforced polymer | Strong, modern; adaptability and customizability |
Custom-Fit Desk | Ergonomic design; adjustable components; customized workspace | Wood-polymer composite | Functional; comfortable; personalized |
Efficiency Enhancements in Furniture Manufacturing
D printing is revolutionizing furniture manufacturing by streamlining processes, reducing costs, and enhancing design flexibility. The technology’s ability to create intricate shapes and customized components directly impacts the overall efficiency of the production chain. This transformative approach is reshaping the industry’s traditional methods and paving the way for greater efficiency and innovation.
Streamlined Manufacturing Process
D printing’s inherent nature allows for a more direct and less complex manufacturing process. Instead of relying on multiple steps and intermediary parts, designs are often realized in a single, continuous operation. This direct creation of components, often complex and intricate, eliminates the need for intermediate tooling, reducing lead times and the associated logistical complexities. For example, a chair’s intricate backrest, once requiring multiple molding and assembly steps, can now be produced directly with 3D printing, significantly accelerating the process.
Reduced Production Time and Costs
D printing dramatically reduces production time by bypassing traditional manufacturing steps. Prototyping and testing are expedited, allowing for quicker iteration cycles and the incorporation of customer feedback. This acceleration often translates to substantial cost savings. Furthermore, by eliminating the need for costly tooling and labor-intensive processes, 3D printing directly impacts manufacturing costs. The reduction in material waste also contributes to cost savings, as discussed in the following section.
Reduced Material Waste
D printing’s ability to produce customized parts with minimal material overhang leads to substantial reductions in material waste. This precision-driven approach contrasts sharply with traditional manufacturing methods, where significant material is often lost in cutting, shaping, and assembly. In the case of complex, multi-part furniture pieces, 3D printing can optimize material use by combining components into single, seamless structures.
This is particularly evident in projects that previously required multiple material types, as 3D printing can use a single material for multiple components, thus reducing waste from material transitions.
Improved Accuracy and Precision
D printing allows for high levels of accuracy and precision in manufacturing. The technology’s inherent ability to produce complex geometries with tight tolerances leads to more accurate and consistent parts. This precision minimizes the need for post-processing adjustments, leading to improved quality control and reduced rework. The consistent accuracy inherent in 3D printing is crucial for achieving the desired aesthetic in furniture design, as well as for maintaining dimensional tolerances required for assembly.
Summary Table of Efficiency Gains
Efficiency Gain | Description | Impact |
---|---|---|
Reduced Production Time | Eliminates intermediary steps, accelerates prototyping, and allows faster iteration cycles. | Significant reduction in lead times and quicker delivery of products to market. |
Reduced Production Costs | Eliminates costly tooling, minimizes material waste, and reduces labor costs. | Lower overall manufacturing expenses and increased profitability. |
Reduced Material Waste | Produces customized parts with minimal material overhang, optimizing material use. | Significant cost savings and a more sustainable manufacturing approach. |
Improved Accuracy and Precision | Produces complex geometries with tight tolerances, minimizing the need for post-processing adjustments. | Higher quality products, improved consistency, and reduced rework. |
Materials Used in 3D Printing Furniture
D printing, with its ability to create complex geometries, is revolutionizing furniture manufacturing. A key aspect of this revolution lies in the diverse range of materials suitable for 3D printing, each offering unique properties that influence design, functionality, and environmental impact. The selection of materials is crucial for achieving the desired aesthetic and performance characteristics in the final product.
Material Properties and Characteristics
The properties of 3D printing materials directly affect the final product’s strength, durability, and aesthetic appeal. Materials with high tensile strength are ideal for load-bearing components, while materials with good flexibility might be better suited for decorative elements. Consideration must also be given to the material’s resistance to wear and tear, its ability to withstand environmental factors, and the ease of finishing and painting.
Common 3D Printing Materials
A variety of materials are used in 3D printing furniture, each with its own set of advantages and disadvantages. The choice of material significantly influences the design possibilities and the overall product quality.
- Polylactic Acid (PLA): PLA is a widely used bioplastic derived from renewable resources like corn starch. It’s known for its relatively low cost, ease of printing, and good mechanical strength. PLA is generally suitable for prototypes and decorative items, but its performance may not be ideal for high-stress applications. Its biodegradability is a major environmental plus. However, it may not be as durable as other materials.
- Acrylonitrile Butadiene Styrene (ABS): ABS is a robust thermoplastic polymer with good impact resistance and dimensional stability. It is a popular choice for furniture components that require durability, such as chair legs or tabletops. ABS is more resistant to heat and chemicals compared to PLA, making it suitable for various applications. However, ABS may be more challenging to print and often has a less aesthetically pleasing finish.
- Polycarbonate (PC): PC is a high-impact, transparent thermoplastic known for its strength and resistance to high temperatures. It is often used in 3D printed furniture components that require exceptional impact resistance or need to be visually transparent, such as protective panels or decorative accents. The high cost and potential for warping during printing are considerations.
- Carbon Fiber-Reinforced Polymers (CFRP): CFRP offers exceptional strength-to-weight ratios and stiffness. Its use in 3D printed furniture enables the creation of lightweight yet durable components. The high cost and specialized printing equipment required are major limitations.
- Wood-based Materials: 3D printing is being used to incorporate wood fibers and other natural materials into composite filaments. This creates a combination of the aesthetic appeal of wood with the design freedom of 3D printing. The properties and environmental impact vary based on the specific composite blend.
Environmental Impact of Materials
The environmental impact of 3D printing materials is a growing concern. Some materials are derived from petroleum-based resources, contributing to carbon emissions, while others are bio-based, minimizing this impact. The choice of material can directly influence the sustainability of the entire production process.
Comparison of 3D Printing Materials
The table below summarizes the characteristics of common 3D printing materials for furniture.
Material | Strength | Durability | Aesthetics | Environmental Impact | Cost |
---|---|---|---|---|---|
PLA | Moderate | Good | Good | Low | Low |
ABS | High | Excellent | Moderate | Medium | Moderate |
PC | High | Excellent | Excellent | High | High |
CFRP | Very High | Excellent | Excellent | Medium-High | High |
Wood-based | Variable | Good | Excellent | Low-Medium | Variable |
Challenges and Future Trends
The integration of 3D printing into furniture manufacturing presents exciting opportunities but also poses certain challenges. Overcoming these hurdles is crucial for realizing the full potential of this transformative technology. Understanding the limitations of current methods and anticipating future advancements is essential for successful implementation and sustained growth in the industry.Current 3D printing techniques for furniture production face limitations that must be addressed to expand their practical application.
These limitations impact factors like production scale, material selection, and design complexity, all crucial for large-scale furniture manufacturing.
Potential Challenges
The current capabilities of 3D printing for furniture manufacturing are not without limitations. Material availability, particularly for complex designs and large-scale production, remains a significant constraint. Furthermore, the high cost of specialized 3D printing equipment, along with the technical expertise needed to operate and maintain it, often acts as a barrier to entry for smaller furniture manufacturers. The speed of production for complex designs can be slower than traditional methods, affecting the overall manufacturing process.
Limitations of Current Technologies
Several limitations restrict the wider adoption of 3D printing in furniture production. The intricate nature of some furniture designs often exceeds the capabilities of current 3D printing technologies, leading to challenges in producing fine details and complex geometries without compromising structural integrity. The availability of materials suitable for furniture applications with desired properties like strength, durability, and aesthetics remains a significant constraint.
Current 3D printing processes often struggle to create large-scale furniture pieces, limiting the potential for widespread application in the industry. Moreover, the need for post-processing steps, like finishing and assembly, can add to the complexity and cost of the manufacturing process.
Future Trends in 3D Printing Technology
Advancements in 3D printing technologies are constantly evolving, promising significant improvements in the future. Increased material options, including advanced composites and bio-based materials, are expected to open up new possibilities for furniture design and manufacturing. Further development of printing techniques like multi-material 3D printing could allow for more complex designs and integrated components. Improved printing speed and scalability are crucial to reduce production time and costs, making 3D printing more competitive with traditional methods for large-scale furniture manufacturing.
Expected Impact on the Furniture Industry
The impact of 3D printing on the furniture industry is expected to be significant, fostering both challenges and opportunities. The potential for mass customization of furniture designs will allow customers to create unique pieces tailored to their individual preferences. This will likely lead to a shift in the furniture market, from mass production to personalized and on-demand production.
The development of new materials and processes will lead to the creation of innovative furniture designs and aesthetics.
Possible Future Applications
D printing has the potential to revolutionize various aspects of furniture production. Customization and on-demand manufacturing will become increasingly important, allowing for the production of unique furniture pieces tailored to specific needs and preferences. The creation of furniture with complex shapes and intricate designs, currently challenging to manufacture using traditional methods, will become more feasible. Integration with other manufacturing technologies, such as robotic assembly, will further enhance the efficiency and productivity of the furniture production process.
Furthermore, the development of modular furniture components, created and assembled using 3D printing, could lead to sustainable and adaptable furniture solutions.
Case Studies of 3D Printed Furniture
Exploring successful implementations of 3D printing in furniture manufacturing reveals valuable insights into the technology’s potential and challenges. These case studies offer practical examples, demonstrating how innovative design, efficient production, and strategic marketing can drive adoption and success in this evolving sector.
Successful Implementations
Several companies have successfully integrated 3D printing into their furniture production processes. These implementations demonstrate the potential for customized designs, rapid prototyping, and reduced lead times. The diverse applications and outcomes highlight the adaptability of 3D printing to various furniture manufacturing needs.
Company/Project | Design Focus | Production Strategy | Marketing Approach | Key Takeaways |
---|---|---|---|---|
“Modular Furniture Solutions” | Customizable modular sofas and armchairs. The design focused on providing flexibility in arrangement and size, catering to diverse living spaces. | Utilizing a combination of fused deposition modeling (FDM) and selective laser sintering (SLS) for different components. This allowed for rapid prototyping and efficient production of complex geometries. Specialized software was employed to optimize the print paths and reduce material waste. | Highlighting the modular nature and customization options. Showcasing how different configurations could enhance the aesthetic appeal of a living space, emphasizing the flexibility of the pieces. Partnerships with interior designers and architects were crucial in reaching target customers. | Successfully integrated 3D printing for a wide range of furniture components, showcasing the ability to create intricate shapes and complex joints. Demonstrated that customization is a key driver for consumer interest. |
“Artisanal 3D Printed Tables” | Creating unique, sculptural coffee tables and side tables with intricate designs. Focus was on using natural materials and innovative aesthetics. | Leveraged SLA (stereolithography) for precision and detail in the designs, focusing on high-quality finishes. The production process included meticulous post-processing steps, such as sanding and polishing, to achieve the desired aesthetic. | Positioning the tables as high-end artisanal pieces. Highlighting the craftsmanship involved in both the 3D printing and post-processing. Utilizing online platforms and collaborations with art galleries and interior design showrooms for marketing. | Demonstrated the capability of 3D printing to create high-quality, intricate furniture pieces, while maintaining an artisanal aesthetic. |
“Eco-Friendly Chair Project” | Developing a chair design using bio-based polymers. The project aimed at producing a sustainable and affordable furniture solution. | Used FDM printing with bio-based filaments. The production process was optimized for minimal material usage and waste. | Emphasizing the sustainability aspect of the design and materials. Partnered with environmental organizations to promote the project. | Successfully demonstrated the potential for environmentally friendly 3D printed furniture. |
Key Factors for Success
The success of these case studies is attributable to several key factors. Careful consideration of design, material selection, and production strategies are critical to achieving positive outcomes. Efficient marketing campaigns targeting the right audience are essential to successful product launch.
- Strategic Design: Adapting the design to leverage the capabilities of 3D printing. Focusing on complex geometries, customizability, and innovative aesthetics.
- Optimized Production: Implementing efficient production strategies, optimizing print parameters, and ensuring appropriate post-processing steps to achieve desired quality and finish. Employing appropriate 3D printing technologies and materials for the specific designs.
- Targeted Marketing: Developing a clear and compelling marketing strategy that emphasizes the unique value proposition of the 3D printed furniture. Highlighting customization, sustainability, or other key selling points.
Wrap-Up: Revolutionary 3D Printing Techniques Transform Furniture Manufacturing Efficiency
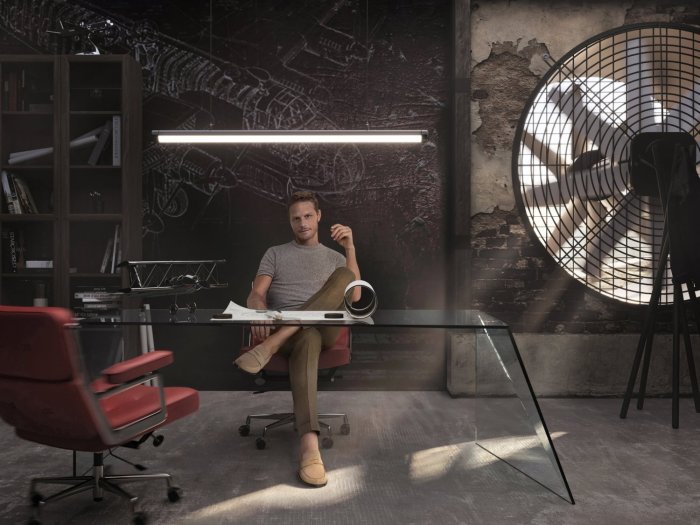
Source: cgifurniture.com
In conclusion, the integration of 3D printing into furniture manufacturing presents a significant opportunity for innovation and efficiency. While challenges remain, the potential for customized designs, reduced production costs, and minimized material waste is substantial. The future of furniture production is undoubtedly being reshaped by these revolutionary technologies. This report has explored the key facets of this transformative shift, highlighting the immense potential for the future of furniture manufacturing.
Clarifying Questions
What are the common materials used in 3D printing furniture?
Common materials include plastics like PLA and ABS, as well as metal alloys and composites. The choice depends on the desired strength, durability, and aesthetic appeal of the final product.
How does 3D printing reduce material waste compared to traditional methods?
3D printing enables precise material usage, eliminating excess material commonly found in traditional woodworking and casting. This translates to lower waste and greater cost-effectiveness.
What are some limitations of current 3D printing technologies in furniture production?
Current 3D printing technologies might face limitations in terms of the size and complexity of furniture pieces. Additionally, the cost of specialized printers and materials can be a barrier for some manufacturers.
How does 3D printing impact furniture design freedom?
3D printing empowers designers with greater freedom to create intricate and complex designs previously unattainable with traditional methods. The possibilities for unique and personalized pieces are practically limitless.