Raw Materials Challenge Industrial Perfection explores the critical interplay between the availability and quality of raw materials and the pursuit of industrial excellence. This intricate relationship demands a deep understanding of sourcing, processing, and optimization strategies to navigate potential limitations and maximize efficiency. From identifying specific challenges in various industries to showcasing innovative solutions, this comprehensive analysis provides a roadmap for achieving industrial perfection while minimizing environmental impact.
The exploration delves into the diverse challenges faced by industries relying on raw materials, examining how quality, scarcity, and sustainability intertwine with achieving industrial perfection. This discussion highlights the importance of meticulous material selection, consistent quality control, and the strategic application of technology in optimizing processes and overcoming obstacles. Further, it presents a balanced perspective on the crucial role of sustainable practices within the supply chain.
Defining the Challenge: Raw Materials Challenge Industrial Perfection
The Raw Materials Challenge encompasses the multifaceted difficulties inherent in sourcing, processing, and utilizing raw materials for industrial production. It’s a complex issue impacting various sectors, from agriculture to manufacturing, and demanding innovative solutions to ensure continued productivity and economic growth. The challenge is not simply about finding raw materials; it’s about securing reliable, sustainable, and cost-effective sources while mitigating environmental impact.The process of obtaining raw materials often presents significant hurdles.
Geographical limitations, political instability in producing regions, and environmental regulations can all disrupt supply chains. Furthermore, fluctuating market prices and unpredictable global events can create volatility in raw material costs, impacting profitability and production schedules. This underscores the critical need for robust supply chain management strategies and diversification of sources.
Raw Material Sourcing and Utilization Difficulties
Securing consistent supplies of raw materials is a constant challenge for many industries. Geopolitical factors, such as trade wars and sanctions, can significantly impact the availability and cost of raw materials. Furthermore, environmental concerns and ethical considerations play an increasingly important role in sourcing decisions. This leads to complex trade-offs between economic viability, environmental sustainability, and social responsibility.
For instance, the increasing demand for rare earth minerals for electronics production has led to concerns about mining practices in certain regions.
Industries Facing Raw Material Challenges
Numerous industries face significant raw material challenges. The automotive sector, heavily reliant on metals like iron and aluminum, is particularly vulnerable to price fluctuations and supply disruptions. The electronics industry, needing rare earth elements and precious metals, confronts the issue of sourcing materials responsibly. Furthermore, the construction sector, using a wide range of materials, experiences variability in the cost and availability of concrete ingredients.
Impact of Raw Material Scarcity on Industrial Production
Raw material scarcity directly impacts industrial production in several ways. Production timelines can be extended due to delays in sourcing. Increased costs can reduce profitability and competitiveness, potentially leading to job losses. Furthermore, scarcity can spur innovation, encouraging the development of alternative materials and production processes. The rise in demand for bio-based plastics, for example, is a direct response to concerns about fossil fuel-derived plastics.
Different Types of Raw Materials and Their Challenges
The availability and cost of raw materials vary greatly depending on their type. Factors such as geological formations, extraction methods, and processing requirements influence the ease and cost of acquiring them. The following table illustrates potential challenges and impacts:
Raw Material Type | Potential Challenges | Impact on Industry |
---|---|---|
Metals (Iron, Aluminum) | Fluctuating prices, geopolitical instability in producing regions, environmental regulations related to mining. | Increased production costs, potential supply disruptions, reduced competitiveness in global markets. |
Rare Earth Minerals | Ethical concerns regarding mining practices, geopolitical tensions over control of resources, limited availability and processing capacity. | Increased costs for electronics, limited innovation in certain technologies, potential for supply chain bottlenecks. |
Fossil Fuels (Oil, Natural Gas) | Fluctuating prices, geopolitical instability in producing regions, environmental concerns related to emissions. | Increased energy costs, potential for supply disruptions, pressure to adopt renewable energy sources. |
Agricultural Products (Cotton, Wood) | Climate change impacts, fluctuating yields, concerns about deforestation and land use practices. | Variable costs, potential for food security issues, need for sustainable agriculture practices. |
Exploring Industrial Perfection
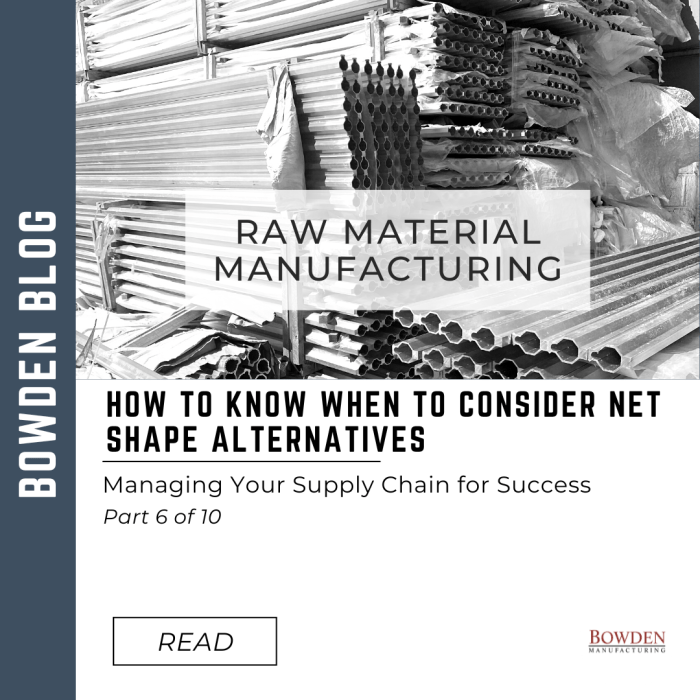
Source: bowdenmfg.com
Industrial perfection in manufacturing transcends mere efficiency; it represents a pursuit of optimal processes, unwavering quality, and minimal waste. This exploration delves into the multifaceted meaning of industrial perfection, examining its key characteristics and the crucial stages involved in achieving it. Understanding these aspects is essential for businesses aiming to enhance their operations and gain a competitive edge.Industrial perfection, in the context of manufacturing, signifies a state where processes are consistently executed with minimal defects, maximum output, and optimized resource utilization.
This ideal entails a comprehensive understanding of every stage, from raw material procurement to final product delivery, aiming to eliminate bottlenecks, reduce variability, and ensure a seamless flow.
Defining Characteristics of an Industrially Perfect Process
A perfectly executed industrial process exhibits several key characteristics. Firstly, it is highly reliable, consistently producing high-quality products with minimal defects. Secondly, it is highly efficient, utilizing resources effectively and minimizing waste. Thirdly, it is adaptable, capable of responding swiftly to changing demands and market trends. Finally, it is safe, prioritizing worker well-being and adhering to environmental regulations.
These qualities are crucial for long-term sustainability and profitability.
Stages of Industrial Processes and their Role in Perfection
Industrial processes typically comprise several distinct stages. The initial stage involves raw material procurement, emphasizing sourcing high-quality, consistent materials. Subsequent stages include manufacturing, assembly, quality control, and packaging. Each stage plays a critical role in the overall process; deficiencies in any stage can negatively impact the final product. Optimal execution throughout all stages is crucial for achieving industrial perfection.
Approaches to Industrial Optimization
Various approaches exist for optimizing industrial processes. Lean manufacturing, for instance, focuses on eliminating waste and streamlining operations. Six Sigma emphasizes reducing variation and improving quality. These approaches often complement each other, leading to comprehensive optimization strategies.
Comparison of Optimization Strategies
Optimization Strategy | Description | Benefits |
---|---|---|
Lean Manufacturing | Focuses on eliminating waste (muda) in all forms, from overproduction to unnecessary transportation. It emphasizes value stream mapping and continuous improvement. | Increased efficiency, reduced lead times, and lower costs. |
Six Sigma | Data-driven approach to process improvement. Aims to reduce defects and variations by using statistical methods and tools. | Higher quality products, improved consistency, and reduced defects. |
Agile Manufacturing | Adaptable manufacturing approach allowing for rapid response to changing customer needs and market conditions. Utilizes flexible resources and short production cycles. | Improved responsiveness to customer demand, faster time-to-market, and enhanced flexibility. |
Digitalization | Implementation of digital technologies like automation, machine learning, and IoT to enhance efficiency and decision-making. | Enhanced real-time monitoring, improved predictive maintenance, and data-driven insights. |
The Intersection of Raw Materials and Industrial Perfection
Raw materials are the foundation of any industrial process. Their quality, consistency, and availability directly impact the efficiency, cost, and ultimately, the perfection of the final product. Understanding the intricate relationship between raw materials and industrial processes is crucial for achieving excellence in manufacturing.Precise material selection and consistent quality throughout the supply chain are paramount to achieving industrial perfection.
This involves careful consideration of not only the intrinsic properties of the raw material but also its impact on downstream processes. Innovations in sourcing and processing techniques can mitigate challenges posed by inconsistent raw material quality, leading to greater efficiency and higher product quality.
Impact of Raw Material Quality on Industrial Processes
Raw material quality significantly affects various stages of industrial processes. Variations in composition, impurities, or physical properties can lead to inconsistencies in product quality, increased waste, and higher production costs. For instance, variations in the chemical composition of steel can lead to differences in strength, ductility, and corrosion resistance, impacting the final product’s performance. Similarly, inconsistencies in the moisture content of wood can affect its dimensional stability and strength, impacting furniture production.
These examples highlight the direct link between raw material quality and the quality of the final product.
Importance of Precise Material Selection
Precise material selection is critical for achieving industrial perfection. The right raw material choice optimizes process efficiency and minimizes waste. A thorough understanding of the specific requirements of each industrial process is essential. This includes considering factors such as strength, durability, chemical resistance, and cost-effectiveness. Selecting the appropriate raw material for a particular application reduces the likelihood of defects and ensures that the final product meets the desired specifications.
Ensuring Consistent Raw Material Quality Throughout the Supply Chain
Maintaining consistent raw material quality throughout the supply chain is a crucial aspect of industrial perfection. This requires robust quality control measures at every stage, from sourcing to processing. Implementing standardized testing procedures, rigorous quality checks, and transparent communication with suppliers are vital. Advanced technologies, such as advanced analytics and sensor systems, can be leveraged to monitor and track raw material quality in real-time, enabling proactive adjustments and minimizing variations.
Continuous improvement initiatives and feedback loops are essential to address any identified quality issues and maintain consistency.
Innovative Solutions to Overcome Raw Material Challenges
Innovations in sourcing and processing can significantly overcome raw material challenges. For instance, the development of alternative materials with improved properties can address shortages or limitations of traditional materials. The use of advanced technologies, such as 3D printing, allows for the creation of customized components using diverse materials, increasing flexibility and efficiency. Furthermore, recycling and reuse programs can minimize environmental impact and reduce reliance on virgin raw materials.
These solutions not only enhance industrial processes but also contribute to sustainability efforts.
Relationship Between Raw Material Characteristics and Industrial Process Efficiency
Raw Material Characteristic | Impact on Process Efficiency | Examples |
---|---|---|
Purity | Reduced defects, increased yield, lower rework costs | High-purity silicon for semiconductor manufacturing |
Homogeneity | Consistent product quality, predictable process outcomes | Uniformly mixed concrete for construction |
Dimensional Stability | Reduced dimensional errors, improved fit, increased precision | Precisely sized lumber for furniture construction |
Strength | Higher load-bearing capacity, reduced material usage | High-strength steel for bridges and buildings |
Chemical Resistance | Extended product lifespan, minimized corrosion | Corrosion-resistant alloys for chemical processing equipment |
Cost-Effectiveness | Reduced production costs, increased profitability | Recycled materials for various applications |
Strategies for Overcoming the Challenge
Optimizing industrial processes in the face of fluctuating raw material availability and cost is crucial for maintaining profitability and competitiveness. Effective strategies must address waste reduction, technological advancements, innovative substitutions, and sustainable supply chains to ensure long-term success. This section Artikels key approaches for achieving industrial perfection while navigating raw material challenges.Addressing raw material challenges necessitates a multi-faceted approach that considers the entire supply chain, from sourcing to processing.
This involves proactive measures to minimize disruptions, optimize resource utilization, and ensure environmental responsibility. Companies must embrace a culture of continuous improvement to adapt to dynamic market conditions and maintain a competitive edge.
Optimizing Industrial Processes
Strategies for optimizing industrial processes require a comprehensive understanding of raw material properties, processing techniques, and potential waste points. By carefully evaluating these elements, companies can identify areas for improvement and implement tailored solutions.
- Process Optimization Techniques: Implementing lean manufacturing principles, such as value stream mapping and 5S methodology, can significantly reduce waste and improve efficiency. Analyzing process bottlenecks and implementing targeted improvements can optimize throughput and minimize material loss. For example, a steel manufacturer could analyze the process of rolling steel sheets, identifying areas where scrap is generated and implementing adjustments to minimize waste.
- Material Flow Analysis: Understanding the flow of materials throughout the production process is crucial for identifying areas of potential waste. By mapping the entire process and identifying points where materials are lost or wasted, companies can implement corrective measures. This includes analyzing the material’s journey from receiving to processing, identifying material loss during storage, and optimizing handling procedures.
Reducing Waste and Maximizing Material Utilization
Minimizing waste and maximizing material utilization are key strategies for enhancing efficiency and profitability. This approach encompasses a broad range of techniques, from process modification to the adoption of advanced materials.
- Waste Reduction Strategies: Implementing closed-loop systems and recycling programs can drastically reduce waste and promote resource recovery. Companies can use waste streams as secondary inputs, reducing dependence on virgin materials. For instance, a paper manufacturer could establish a program to recycle used paper products, reducing the demand for raw wood pulp.
- Material Substitution and Recycling: Exploring alternative materials that offer similar performance characteristics at a lower cost can reduce dependence on expensive or scarce raw materials. Developing robust recycling processes is crucial for closing the loop and minimizing environmental impact. For example, in the construction industry, using recycled aggregates in concrete can decrease reliance on virgin materials and reduce waste.
Technology in Raw Material Sourcing and Processing
Technological advancements are revolutionizing raw material sourcing and processing, enabling greater efficiency and sustainability. These technologies provide opportunities to optimize every stage of the process, from discovery to production.
- Advanced Materials Analysis: Utilizing advanced analytical techniques, such as X-ray diffraction and spectroscopy, allows for precise characterization of raw materials, optimizing processing and reducing waste. This detailed understanding of material properties allows companies to tailor processing parameters to specific raw materials, improving efficiency.
- Digitalization and Automation: Implementing digital technologies, such as data analytics and automation systems, can enhance the efficiency of raw material sourcing and processing. This can streamline processes, reduce manual intervention, and enhance overall precision. For instance, a mining company can leverage digital twins of mines to optimize extraction strategies and predict potential challenges.
Sustainable Practices in the Supply Chain
Integrating sustainable practices into the supply chain is vital for long-term profitability and responsible resource management. Companies must prioritize environmental stewardship throughout the entire process.
- Ethical Sourcing Practices: Ensuring ethical sourcing of raw materials by promoting fair labor practices, reducing environmental impact, and avoiding conflict minerals is crucial. This involves scrutinizing the supply chain for any potential ethical concerns and working to mitigate risks. For example, a textile company could partner with suppliers who adhere to strict labor standards.
- Environmental Responsibility: Implementing environmentally friendly practices, such as minimizing water usage and reducing carbon emissions, is crucial for long-term sustainability. This encompasses a holistic approach that involves evaluating and minimizing environmental impacts throughout the entire process. For instance, a chemical manufacturer can invest in renewable energy sources and implement water recycling systems to minimize their environmental footprint.
Illustrative Examples
Real-world examples demonstrate the practical application of strategies for achieving industrial perfection when dealing with raw material challenges. These examples highlight the innovative solutions implemented by successful companies, the complexities inherent in raw material acquisition, and the profound impact of raw material quality on the final product.
A Successful Case Study of Overcoming Raw Material Challenges
Consider the case of a high-end automotive manufacturer who faced consistent fluctuations in the quality of a specific alloy used in their engine components. This inconsistency led to production delays and increased costs due to rework and scrap. The company addressed this by implementing a robust supplier relationship management system. This involved detailed quality audits of potential suppliers, stringent testing protocols for incoming raw materials, and establishing clear communication channels to address issues proactively.
By meticulously controlling the entire supply chain, the manufacturer stabilized raw material quality, leading to improved production efficiency and enhanced product reliability. This resulted in reduced costs and increased customer satisfaction.
Innovative Strategies for Achieving Industrial Perfection Despite Raw Material Limitations, Raw Materials Challenge Industrial Perfection
A company producing specialized electronics components faced limitations in accessing a critical rare earth element. To overcome this challenge, they pursued a multi-pronged approach, focusing on both innovation and resourcefulness. Firstly, they invested in research and development to explore alternative materials that could substitute the rare earth element in their manufacturing process. Simultaneously, they actively engaged in collaborative projects with research institutions to accelerate the development of these alternative materials.
The company also actively explored the possibility of sourcing the rare earth element from secondary markets and recycled sources, demonstrating a commitment to sustainable practices. These innovative strategies allowed them to achieve industrial perfection while minimizing their reliance on the limited resource.
Challenges Faced by an Industry in Obtaining Specific Raw Materials
The mining industry frequently faces significant challenges in obtaining specific raw materials. These challenges often involve fluctuating market prices, geographical limitations, political instability in resource-rich regions, and environmental regulations. For example, the demand for lithium, a critical component in battery technology, has skyrocketed, leading to increased competition and price volatility. This, coupled with strict environmental regulations regarding mining practices, poses substantial hurdles for companies seeking to acquire lithium at a sustainable rate and cost.
Raw Material | Specific Challenges |
---|---|
Lithium | High demand, price volatility, environmental regulations |
Rare Earth Elements | Limited supply, geopolitical factors, environmental concerns |
Specific Metals (e.g., Titanium) | Complex extraction processes, energy-intensive production, potential pollution |
Impact of Raw Material Quality on a Manufacturing Process
Consider the production of high-precision metal components, such as those used in aerospace applications. The quality of the raw metal significantly impacts the final product’s performance. Impurities in the raw material can lead to inconsistencies in the component’s dimensional accuracy, strength, and corrosion resistance. Defects in the raw material, such as inclusions or voids, can manifest as cracks or failures in the final product, potentially leading to catastrophic consequences.
Thus, maintaining strict quality control over the raw material is crucial for ensuring the reliability and safety of the manufactured product.
“Maintaining consistent raw material quality is critical to achieving industrial perfection in high-precision manufacturing.”
Benefits of Sustainable Raw Material Sourcing and Processing
Adopting sustainable practices in raw material sourcing and processing offers numerous benefits. These include reduced environmental impact, enhanced brand reputation, improved supply chain resilience, and cost savings through efficient resource utilization. Companies that prioritize sustainable practices often demonstrate a strong commitment to environmental responsibility, which can attract environmentally conscious consumers and investors. Furthermore, sustainable sourcing strategies can help mitigate risks associated with supply chain disruptions and volatile raw material markets.
Visual Representation of Concepts
Visual representations are crucial for understanding complex industrial processes and the impact of raw materials. They provide a concise and accessible way to illustrate the flow of materials, highlight critical stages, and demonstrate the relationships between various factors. This section details several visual representations that can effectively communicate these concepts.
Flow of Raw Materials Through an Industrial Process
A flowchart would effectively depict the journey of raw materials. The diagram would begin with the source of the raw material, showcasing its initial state. Subsequent stages would be represented by boxes or shapes, each illustrating a specific transformation or process. Arrows would connect these stages, indicating the direction of material flow. This visualization would highlight the various stages involved, from extraction or procurement to the final product.
For example, a diagram depicting the flow of iron ore from the mine to the steel mill, through smelting and rolling, would show a clear path.
Stages of a Manufacturing Process and Raw Material Impact
A series of interconnected diagrams, or a multi-panel graphic, could illustrate the different stages of a specific manufacturing process. Each panel would represent a stage, such as material preparation, shaping, coating, and quality control. Within each panel, a graphic would represent the specific raw materials used and their contribution to that stage. For instance, the panel for shaping would showcase the raw material’s properties (e.g., malleability) influencing the shaping process and the final product’s dimensions.
The panel on coating would illustrate the effect of the coating material on the durability of the final product.
Relationship Between Raw Material Quality and Product Quality
A scatter plot or a bar graph would effectively illustrate the relationship between raw material quality and product quality. The x-axis would represent a quality metric of the raw material (e.g., purity, strength, or consistency), and the y-axis would represent a corresponding quality metric of the final product (e.g., durability, strength, or performance). This visual would showcase a strong correlation between higher raw material quality and superior product quality.
A trend line on the graph would visually represent the correlation.
Efficiency Gains Through Raw Material Optimization
A before-and-after comparison using charts would highlight the efficiency gains achieved through raw material optimization. One chart could illustrate the resource consumption (e.g., energy, water) associated with a specific process using a less optimized raw material. The other chart would display the same process but with optimized raw materials, showing a marked reduction in resource consumption. The comparison would clearly demonstrate the potential for significant efficiency improvements through raw material optimization.
This could be visualized with stacked bar charts.
Environmental Impact of Different Raw Material Sourcing Methods
A stacked bar chart, segmented by raw material sourcing method (e.g., sustainable forestry, conventional mining), could visually represent the environmental impact. Each segment of the bar would represent a different environmental factor (e.g., carbon emissions, water usage, waste generation). The chart would clearly illustrate the varying environmental footprints associated with different raw material sourcing methods, enabling a comparison.
Conclusion
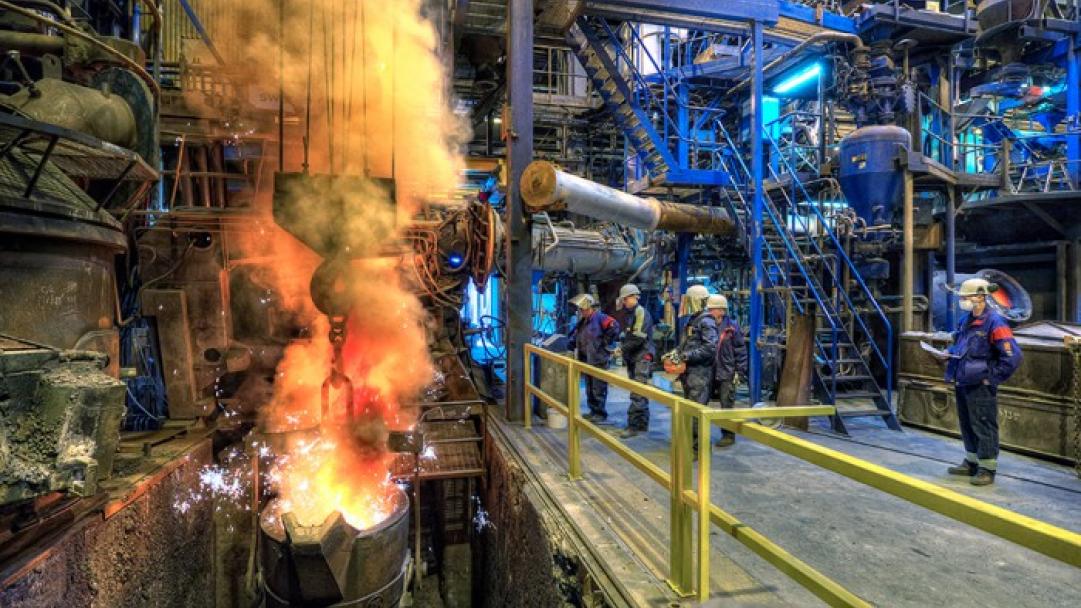
Source: swerim.se
In conclusion, achieving industrial perfection in the face of raw material challenges necessitates a multifaceted approach. The interplay between material quality, sourcing strategies, and process optimization is central to this discussion. This analysis underscores the need for innovation, technology adoption, and sustainable practices to ensure both operational excellence and environmental responsibility. Ultimately, overcoming these challenges is not merely about maximizing output but also about ensuring long-term viability and ethical considerations within the industry.
Essential FAQs
What are some common raw material challenges faced by industries?
Fluctuating prices, supply chain disruptions, and limited availability of specific materials are common challenges. Quality inconsistencies and environmental concerns associated with extraction and processing can also pose significant obstacles.
How can technology improve raw material sourcing and processing?
Advanced technologies like AI and machine learning can optimize material selection and predict potential shortages. Automation can enhance efficiency and consistency in processing, reducing waste and improving quality.
What is the role of sustainability in raw material sourcing?
Sustainable practices in raw material sourcing encompass ethical considerations, minimizing environmental impact, and ensuring long-term availability of resources. This includes responsible extraction methods, recycling, and the use of recycled materials.
What are some examples of innovative solutions to overcome raw material challenges?
Innovative solutions can include developing alternative materials, implementing advanced recycling techniques, and optimizing existing processes to reduce material consumption. These solutions require collaboration across industries to address specific challenges effectively.