Imagine a home where the raw beauty of industrial design harmonizes with the lush vibrancy of a tropical landscape. This is the essence of a tropical industrial home, a style that celebrates exposed structures and natural materials. But can this aesthetic be achieved sustainably? The answer lies in carefully selecting eco-friendly materials that not only enhance the design but also minimize environmental impact.
This exploration delves into the possibilities, examining the unique challenges and rewarding opportunities presented by integrating sustainable practices into this increasingly popular architectural style.
From sourcing locally-harvested bamboo for flooring and roofing to repurposing reclaimed metal for accents, the choices are diverse and impactful. We’ll investigate the thermal properties of various materials, their durability in humid climates, and the long-term cost-effectiveness of embracing sustainable building practices. By understanding the interplay between aesthetics, functionality, and environmental responsibility, we can create tropical industrial homes that are both stunning and sustainable.
Defining “Tropical Industrial Home” Architectural Style
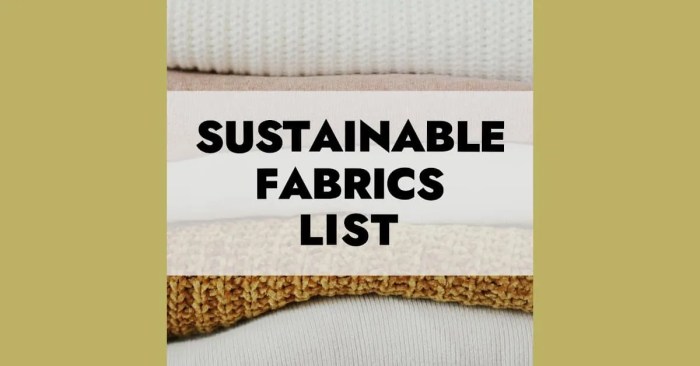
The tropical industrial home style represents a fascinating fusion of contrasting aesthetics: the raw, utilitarian elements of industrial design blended seamlessly with the breezy, natural feel inherent to tropical architecture. This unique style prioritizes open spaces, natural light, and the incorporation of locally sourced, sustainable materials, all while retaining the characteristic industrial touches like exposed metalwork, concrete, and repurposed elements.
The result is a dwelling that is both stylishly modern and environmentally conscious, perfectly suited to warm, humid climates.
Key characteristics of this style include high ceilings to promote airflow, large windows to maximize natural light and ventilation, and a color palette often featuring neutral tones with pops of vibrant tropical colors. The use of industrial materials is not merely decorative; it’s integrated into the structural elements of the home, showcasing the raw beauty of the materials themselves.
This contrasts with purely decorative uses of industrial elements found in other styles.
Materials Commonly Used in Tropical Industrial Homes
Traditional tropical industrial homes often utilize materials that are both durable and readily available in tropical regions. This focus on locally sourced materials reduces the carbon footprint associated with transportation and construction. Common materials include reclaimed wood, often salvaged from old structures and given new life in the design, lending a sense of history and character. Exposed concrete, a hallmark of industrial design, provides a strong, durable base, while metal accents, such as corrugated iron roofing or steel window frames, add a touch of rugged elegance.
Natural stone, readily available in many tropical regions, can be used for flooring and countertops, adding a textural contrast to the other materials. Bamboo, a rapidly renewable resource, can also feature prominently, often used for flooring, screens, or even structural elements in some designs.
Comparison with Other Architectural Styles
The tropical industrial style distinguishes itself from other architectural styles through its unique blend of elements. Unlike purely modern tropical homes, which often prioritize sleek lines and minimalist aesthetics, the tropical industrial style embraces a more raw, textured aesthetic. While both styles incorporate natural light and ventilation, the tropical industrial style retains the industrial feel through the use of exposed materials and a less polished finish.
Similarly, it differs from minimalist designs by its embrace of texture and visible structural elements, rejecting the clean, uncluttered look often associated with minimalism. The industrial aesthetic adds a layer of complexity and visual interest not found in the simpler forms of modern tropical or minimalist homes.
Visual Representation of a Typical Tropical Industrial Home
Imagine a single-story house with a high-pitched, corrugated metal roof, the reddish-brown of the metal contrasting beautifully with the surrounding lush greenery. The walls are a combination of exposed concrete and reclaimed wood panels, the wood’s natural grain visible and adding warmth to the otherwise austere concrete. Large, multi-paned windows, framed in dark metal, allow ample natural light to flood the interior.
The interior space is open and airy, with high ceilings and exposed beams made of reclaimed wood. A polished concrete floor provides a cool, smooth surface, while natural stone accents are used in the kitchen countertops and bathroom vanities. The overall effect is a balance between the raw, industrial elements and the warmth and natural beauty of the tropical setting.
The home sits slightly elevated, perhaps on concrete stilts, further emphasizing the industrial design while allowing for ventilation underneath.
Sustainable Material Sourcing in Tropical Climates
The construction of eco-friendly tropical industrial homes necessitates a careful consideration of material sourcing. The choice of building materials significantly impacts both the environmental footprint of the structure and its long-term performance in the unique challenges presented by tropical climates – high humidity, intense sunlight, and potential for extreme weather events. Prioritizing locally sourced, sustainable materials offers a multitude of benefits, reducing transportation emissions and supporting local economies.
Sustainable material sourcing in tropical regions presents a unique set of opportunities and challenges. The abundance of rapidly renewable resources offers a pathway towards environmentally responsible construction. However, ensuring consistent quality, managing supply chains, and overcoming logistical hurdles requires strategic planning and collaboration.
Readily Available Eco-Friendly Materials for Tropical Climates
Many readily available materials in tropical regions offer excellent sustainability credentials and are well-suited to the climate. Bamboo, for instance, is a rapidly renewable resource with high tensile strength, making it ideal for structural elements and flooring. Thatch, while traditionally used for roofing, offers excellent insulation against heat and offers a unique aesthetic. Rammed earth, a technique using locally sourced soil and stabilized with natural binders, provides excellent thermal mass, regulating indoor temperatures.
Other options include timber from sustainably managed forests, and various types of locally sourced stone. These materials offer a lower embodied carbon footprint compared to materials requiring extensive processing and transportation.
Environmental Impact of Local versus Imported Materials
The environmental impact of using locally sourced materials is considerably lower than that of imported materials. Transportation of building materials contributes significantly to greenhouse gas emissions. Importing materials from distant locations necessitates extensive energy consumption for manufacturing, processing, and transportation, increasing the overall carbon footprint. Conversely, utilizing locally sourced materials reduces transportation distances and emissions, minimizing the environmental impact.
This approach also supports local economies and reduces reliance on global supply chains, promoting regional self-sufficiency. For example, using locally sourced bamboo for scaffolding instead of steel reduces both carbon emissions and reliance on international markets.
Challenges and Opportunities in Sourcing Sustainable Materials in Tropical Regions
Sourcing sustainable materials in tropical regions presents both challenges and opportunities. Challenges include ensuring consistent quality control, managing fluctuating supply, and developing efficient and equitable supply chains. For instance, the unpredictable nature of rainfall can affect the availability of certain materials like bamboo or thatch. However, opportunities exist in developing innovative processing techniques to enhance the durability and lifespan of locally sourced materials.
Investing in research and development to improve the performance of materials like rammed earth or utilizing agricultural waste products as construction materials can unlock new possibilities for sustainable construction. Governmental support through policies promoting sustainable building practices and investment in local industries can further facilitate this transition.
Comparison of Eco-Friendly Material Properties
Material | Durability | Cost | Availability |
---|---|---|---|
Bamboo | High (with proper treatment) | Moderate | High (in many tropical regions) |
Thatch | Moderate (requires regular maintenance) | Low | High (in many tropical regions) |
Rammed Earth | High (with proper compaction and stabilization) | Low | High (dependent on soil quality) |
Sustainable Timber | High | Moderate to High (depending on species and certification) | Moderate (dependent on sustainable forestry practices) |
Locally Sourced Stone | Very High | Variable (depending on type and accessibility) | Variable (dependent on geological location) |
Eco-Friendly Materials for Specific Applications
The judicious selection of eco-friendly materials is paramount in constructing sustainable tropical industrial homes. These materials must not only meet the aesthetic demands of the architectural style but also withstand the unique climatic challenges of tropical regions, such as high humidity, intense rainfall, and strong sunlight. The following sections detail the sustainable application of various materials in different aspects of tropical industrial home design.
Bamboo’s Role in Tropical Industrial Home Construction
Bamboo, a rapidly renewable resource, offers exceptional versatility in tropical industrial home construction. Its inherent strength-to-weight ratio, coupled with its aesthetic appeal, makes it ideal for various applications. Its hollow structure provides excellent insulation, mitigating temperature fluctuations within the home. Furthermore, bamboo’s inherent flexibility allows for innovative design solutions, characteristic of the industrial aesthetic.For flooring, bamboo can be engineered into durable planks, often treated to enhance water resistance and longevity.
Bamboo wall cladding, either in its natural form or treated for durability, offers a visually striking and environmentally friendly alternative to traditional materials. In roofing applications, bamboo can be used to create lightweight and aesthetically pleasing structures, particularly when combined with other sustainable materials like thatch or recycled metal. The rapid growth rate of bamboo ensures its sustainability as a building material, minimizing environmental impact.
For example, a species like
Phyllostachys edulis* (Moso bamboo) is known for its fast growth and strength, making it an excellent choice for structural elements.
Recycled Wood Applications in Tropical Industrial Homes
Recycled wood, salvaged from demolished structures or reclaimed from other sources, presents a sustainable alternative to newly harvested timber. Its inherent character, often marked by age and wear, adds to the unique aesthetic of tropical industrial design. The use of reclaimed wood reduces deforestation and minimizes the environmental impact associated with timber harvesting and processing.In tropical industrial homes, recycled wood can be used effectively for flooring, wall paneling, and even structural elements, depending on the wood’s condition and strength.
The inherent variations in color and texture add character and authenticity to the design, aligning perfectly with the industrial style’s appreciation for raw, unrefined materials. Proper treatment and preservation techniques are crucial to ensure the longevity of recycled wood in humid tropical environments. For instance, using appropriate sealants and treatments can protect the wood from rot, insect infestation, and water damage.
Reclaimed Materials: Metal and Stone in Tropical Industrial Design
Reclaimed materials, such as metal and stone, bring a unique industrial aesthetic to tropical homes. These materials, often salvaged from industrial sites or demolition projects, possess a distinct character that complements the style’s raw and functional essence. The use of reclaimed materials reduces waste, conserves resources, and minimizes the environmental footprint of construction.Reclaimed metal, such as steel or corrugated iron, can be repurposed for roofing, wall cladding, or decorative accents.
Its durability and resistance to harsh weather conditions make it a practical choice for tropical climates. Reclaimed stone, on the other hand, can be used for flooring, walls, or landscaping features. Its natural texture and variation in color add a rustic and visually appealing element to the design. The inherent thermal mass of stone can also help regulate indoor temperatures, contributing to energy efficiency.
A Section of a Home Using Recycled Materials
Consider a section of a home featuring a recycled metal roof, reclaimed wood flooring, and exposed brick walls. The corrugated iron roof, salvaged from a dismantled factory, provides a durable and weather-resistant covering, reflecting the sun’s rays to reduce heat absorption. The flooring, crafted from reclaimed hardwood planks sourced from an old barn, offers a unique character and warm aesthetic.
The exposed brick walls, salvaged from a demolished building, add texture and a sense of history, creating a visually striking contrast with the metal roofing. This combination of materials showcases the versatility and sustainability of reclaimed materials in tropical industrial home design, highlighting the aesthetic appeal and environmental benefits. The inherent thermal mass of the brick walls helps to regulate indoor temperatures, minimizing the need for air conditioning.
The natural oils in the reclaimed wood flooring offer some inherent pest resistance, and the durability of the metal roofing minimizes maintenance requirements. This design choice exemplifies the synergy between aesthetics and sustainability in tropical industrial architecture.
Impact of Material Choices on Energy Efficiency
The tropical climate presents unique challenges for building design, demanding structures that minimize heat gain and maximize natural ventilation. Material selection plays a crucial role in achieving these goals, directly impacting the energy efficiency of a tropical industrial home and its associated cooling costs. The thermal properties of building materials—their ability to absorb, store, and release heat—determine the internal temperature fluctuations and the energy required to maintain a comfortable living environment.The thermal performance of a building material is typically characterized by its thermal conductivity (k-value), which quantifies the rate at which heat flows through a unit thickness of the material.
A lower k-value indicates better insulation, meaning less heat transfer. This is particularly relevant in tropical regions experiencing high solar radiation and ambient temperatures. Poorly chosen materials can lead to significant overheating, necessitating increased reliance on air conditioning, which contributes to high energy consumption and carbon emissions.
Thermal Performance of Eco-Friendly Materials in Tropical Climates
Straw bale and rammed earth are two examples of eco-friendly materials frequently used in sustainable construction. Straw bale, consisting of tightly packed straw bales encased in a protective layer, exhibits excellent insulation properties due to the air trapped within the straw’s structure. Its low thermal conductivity (approximately 0.04 – 0.06 W/m·K) effectively reduces heat transfer, contributing to a more thermally stable interior.
Rammed earth, on the other hand, possesses a higher thermal mass, meaning it can absorb and release heat slowly. This characteristic helps to moderate temperature swings throughout the day, reducing the need for intense cooling during peak hours. While its thermal conductivity is higher than straw bale (approximately 0.8 – 1.5 W/m·K), its thermal mass acts as a natural buffer against temperature fluctuations.
The effectiveness of each material depends on factors such as the density of the construction, the thickness of the walls, and the local climate conditions. For instance, a thicker rammed earth wall will offer better insulation than a thinner one, similarly, a well-constructed straw bale wall with proper sealing will outperform a poorly constructed one.
Reducing Energy Consumption for Cooling Through Material Selection
Proper material selection significantly reduces energy consumption for cooling in tropical climates. Materials with high thermal resistance, such as bamboo, sustainably harvested timber, and certain types of clay bricks, can effectively reduce heat gain. These materials, combined with appropriate design strategies like shading devices, natural ventilation systems, and thermal mass elements, create a synergistic effect, minimizing the need for mechanical cooling.
For example, a design incorporating thick, rammed earth walls and strategically placed overhangs can significantly reduce the solar heat load on the building, leading to lower cooling demands. Conversely, using materials with low thermal resistance, such as thin metal sheeting, will result in increased heat gain and higher energy consumption for cooling. In a real-world scenario, a home built with rammed earth walls in a hot and humid region might experience a 30-40% reduction in cooling energy consumption compared to a similar home constructed with conventional materials like concrete blocks.
The exact savings depend on several factors, including climate, building design, and occupancy patterns.
Strategies for Optimizing Energy Efficiency Through Material Selection
Effective material selection is key to minimizing energy use. The following strategies can optimize energy efficiency in tropical industrial homes:
The proper selection of materials is crucial for minimizing energy consumption in tropical climates. The following strategies highlight the importance of considering both thermal properties and environmental impact:
- Prioritize materials with low thermal conductivity (k-value) for walls, roofs, and floors to minimize heat transfer.
- Utilize materials with high thermal mass to moderate temperature fluctuations and reduce peak cooling loads.
- Incorporate locally sourced materials to reduce embodied energy and transportation costs.
- Select materials with high reflectivity (albedo) for roofing to reduce solar heat gain.
- Ensure proper insulation and air sealing to prevent heat leakage.
- Consider the embodied carbon of materials, opting for those with lower carbon footprints.
Durability and Maintenance of Eco-Friendly Materials
The longevity and ease of maintenance of eco-friendly building materials in tropical climates are crucial considerations. While often perceived as less durable than conventional options, advancements in processing and design are bridging this gap. Understanding the specific needs of each material is key to ensuring a long-lasting and aesthetically pleasing tropical industrial home. This section will explore the maintenance requirements, lifespan comparisons, and potential challenges associated with various sustainable building materials commonly used in tropical construction.
Maintenance Requirements of Eco-Friendly Materials
The maintenance needs of eco-friendly materials vary considerably. Bamboo, for instance, requires regular treatment with protective oils or sealants to prevent insect infestation and moisture damage, particularly in humid tropical environments. This treatment, typically done every 1-2 years, is crucial for extending the lifespan of bamboo structures. Rammed earth, another popular choice, benefits from periodic sealing to prevent erosion and water damage.
This might involve applying a breathable sealant every 3-5 years, depending on exposure and rainfall. Reclaimed timber, while inherently durable, may require occasional sanding and refinishing to maintain its aesthetic appeal and protect against weathering. The frequency depends on the type of wood and the finish applied. Conversely, materials like recycled plastic lumber generally require minimal maintenance, offering significant advantages in high-humidity regions.
Lifespan and Durability Comparison
Direct comparison of the lifespan of eco-friendly materials to conventional materials requires careful consideration of various factors, including material quality, construction techniques, and environmental conditions. While concrete and steel are known for their longevity, often exceeding 50 years with proper maintenance, eco-friendly alternatives can also achieve comparable lifespans. Bamboo, when properly treated and protected, can last for 20-30 years or even longer in favorable conditions.
Rammed earth structures, with regular maintenance, have demonstrated longevity exceeding 100 years in some cases. Reclaimed timber, depending on its initial condition and the species of wood, can have a lifespan comparable to newly harvested timber, often exceeding 50 years. The durability of recycled plastic lumber often surpasses that of traditional wood, exhibiting high resistance to rot, insect infestation, and weathering, making it a highly durable option for tropical climates.
Challenges in Long-Term Maintenance of Sustainable Materials
Despite their advantages, some eco-friendly materials present unique maintenance challenges. For example, maintaining the structural integrity of rammed earth walls requires careful attention to drainage and preventing water penetration. Damage from heavy rainfall or flooding can significantly impact the lifespan of such structures. Bamboo, while renewable, can be susceptible to termite damage if not properly treated. This requires diligent monitoring and timely intervention to prevent significant structural compromise.
The sourcing and availability of specific sealants and treatments designed for eco-friendly materials might also present challenges in certain regions, potentially increasing maintenance costs. Finding skilled tradespeople experienced in working with these materials can also be a factor in ensuring proper maintenance.
Preventative Maintenance Guide for Eco-Friendly Materials in Tropical Environments
Regular inspection is paramount. A twice-yearly inspection allows for early detection of any issues. This should include checking for signs of insect infestation, water damage, cracking, or deterioration. For bamboo structures, this means checking for signs of splitting or weakening, and promptly addressing any issues. For rammed earth walls, inspect for cracks and ensure proper drainage is maintained.
Regular cleaning is essential to remove dirt, debris, and mold, especially in humid climates. Promptly address any water damage to prevent further deterioration. Consider scheduling professional inspections every 3-5 years for comprehensive assessments and preventative treatments. Regular application of appropriate sealants and protective coatings will extend the life of the materials. Proper ventilation is crucial to prevent mold and mildew growth, particularly in areas with limited airflow.
Cost-Effectiveness of Sustainable Building Practices
The initial investment in eco-friendly materials for tropical industrial homes may seem higher than using conventional materials. However, a comprehensive cost-benefit analysis reveals that sustainable building practices often lead to significant long-term savings, making them a financially prudent choice. This analysis considers not only material costs but also energy efficiency, maintenance, and lifespan.The upfront cost of sustainable materials like bamboo, reclaimed wood, or sustainably harvested timber can exceed the cost of readily available concrete or standard lumber.
However, these eco-friendly options often boast superior durability and require less frequent maintenance, offsetting the higher initial investment over the building’s lifespan. Efficient construction methods, minimizing waste and utilizing prefabricated components, also contribute to cost reduction.
Initial and Long-Term Cost Comparison
A direct comparison between a conventionally built tropical industrial home and one constructed using sustainable materials reveals a nuanced picture. While the initial material costs for a sustainably built home might be 10-15% higher, this is often offset by reduced energy consumption. For example, a home utilizing bamboo framing and natural ventilation strategies may require significantly less air conditioning, resulting in substantial savings on electricity bills over the home’s lifetime.
Moreover, the longer lifespan of durable eco-friendly materials reduces the need for costly repairs and replacements, further contributing to long-term cost savings. Consider a scenario where a conventionally built home requires roof replacement after 20 years at a cost of $10,000, whereas a sustainably built home with a durable, locally-sourced tile roof requires replacement only after 40 years, effectively saving $10,000 over the building’s lifetime.
Potential Cost Savings Through Efficient Material Selection and Construction
Strategic material selection and efficient construction methods are crucial in maximizing cost-effectiveness. For instance, choosing locally sourced materials minimizes transportation costs and supports local economies. Utilizing prefabricated components accelerates the construction process, reducing labor costs and project timelines. Careful planning and design can minimize material waste, further contributing to cost savings. Implementing passive design strategies, such as maximizing natural ventilation and daylighting, reduces reliance on mechanical systems, leading to substantial energy cost savings over the building’s lifetime.
These savings can easily outweigh the higher initial cost of sustainable materials.
Government Incentives and Subsidies for Sustainable Building
Many governments recognize the environmental and economic benefits of sustainable building practices and offer various incentives to encourage their adoption. These incentives can include tax credits, rebates, grants, and low-interest loans specifically for projects incorporating eco-friendly materials and energy-efficient technologies. For example, some regions offer tax breaks for installing solar panels or using locally sourced timber. These financial incentives significantly reduce the upfront cost of sustainable construction, making it more competitive with conventional building methods.
It is crucial to research local and national programs to identify available incentives.
Cost-Benefit Analysis: Conventional vs. Eco-Friendly Home
Let’s consider a hypothetical example. A conventionally built 2000 sq ft tropical industrial home might have an initial construction cost of $200,000, with an estimated annual energy cost of $3000. A comparable home built using sustainable materials, incorporating efficient design and locally sourced materials, might have an initial cost of $220,000 (a 10% increase). However, due to superior insulation and passive design, its annual energy cost might be only $1500.
Over a 30-year period, the conventionally built home would incur $90,000 in energy costs, while the sustainable home would incur $45,000. This represents a net savings of $45,000 for the sustainable home, effectively offsetting the initial higher cost. This analysis is a simplification and actual savings will vary based on location, specific materials, and energy prices.
Visual Representation of Eco-Friendly Design Elements
The aesthetic appeal of eco-friendly materials in a tropical industrial home hinges on a delicate balance: embracing the raw, utilitarian elements of industrial design while softening them with the natural textures and colors of sustainable materials. This juxtaposition creates a space that is both modern and inviting, reflecting a commitment to environmental responsibility without sacrificing style. The inherent beauty of sustainably sourced materials, often enhanced by their unique imperfections, adds character and depth to the design, contrasting beautifully with the clean lines of industrial architecture.
The visual impact of these materials is amplified by their thoughtful integration into both the interior and exterior spaces. The chosen materials not only enhance the visual appeal but also contribute significantly to the overall functionality and comfort of the home.
Interior Design with Eco-Friendly Materials
Imagine stepping into a spacious living area. The polished concrete floor, a hallmark of industrial design, is subtly warmed by large, intricately woven sisal rugs sourced from sustainable farms. These rugs, in earthy tones of beige and brown, provide both comfort and a textural contrast to the cool concrete. The walls, clad in reclaimed wood salvaged from old warehouses, display a rich patina, telling a story of the material’s past life.
Their varied tones of grey and brown, punctuated by the occasional knot hole, create a dynamic visual interest. Custom-built shelving units, crafted from bamboo – a rapidly renewable resource known for its strength and flexibility – hold a curated collection of books and plants. The bamboo’s warm honeyed hue complements the cooler tones of the wood and concrete, adding a touch of organic warmth.
Large windows, maximizing natural light, showcase the lush tropical landscape outside, blurring the lines between indoor and outdoor spaces. The furniture, a mix of vintage industrial pieces and new pieces made from recycled steel and sustainably harvested teak, completes the look, showcasing the seamless integration of recycled and sustainable materials.
Texture and Color in Eco-Friendly Design
The interplay of textures is crucial in creating a visually rich and engaging space. The smooth, cool surface of the polished concrete floor contrasts with the rough, tactile feel of the reclaimed wood walls and the woven sisal rugs. The bamboo shelving offers a slightly more delicate texture, adding another layer of visual complexity. The color palette, predominantly neutral with accents of warm earth tones, contributes to a sense of calm and serenity.
The natural variations in color within the reclaimed wood and sisal rugs add depth and visual interest, preventing the space from feeling monotonous. The use of natural dyes and finishes further enhances the organic aesthetic, avoiding harsh chemicals and contributing to the home’s overall eco-friendliness.
Exterior Design Integration of Sustainable Materials
The exterior of the home showcases the same commitment to sustainable design. The roof is covered in locally sourced, sustainably harvested thatch, providing excellent insulation and blending seamlessly with the tropical environment. The exterior walls, constructed from rammed earth – a mixture of soil, sand, gravel, and a stabilizer – offer superior thermal mass, keeping the interior cool during the day and warm at night.
This material, rendered in a smooth, light-grey finish, complements the natural surroundings. Vertical gardens, incorporating native plants, climb along sections of the walls, adding a vibrant splash of green and providing natural insulation. Large, strategically placed windows and skylights maximize natural light and ventilation, minimizing the need for artificial lighting and air conditioning. The overall effect is one of harmony between the built environment and the natural landscape, demonstrating a commitment to both sustainability and aesthetic excellence.
The landscaping itself uses drought-tolerant native plants, minimizing water consumption. Reclaimed materials, such as recycled metal, are incorporated into the design of fences and other exterior features, further reinforcing the commitment to environmental responsibility.
Final Conclusion
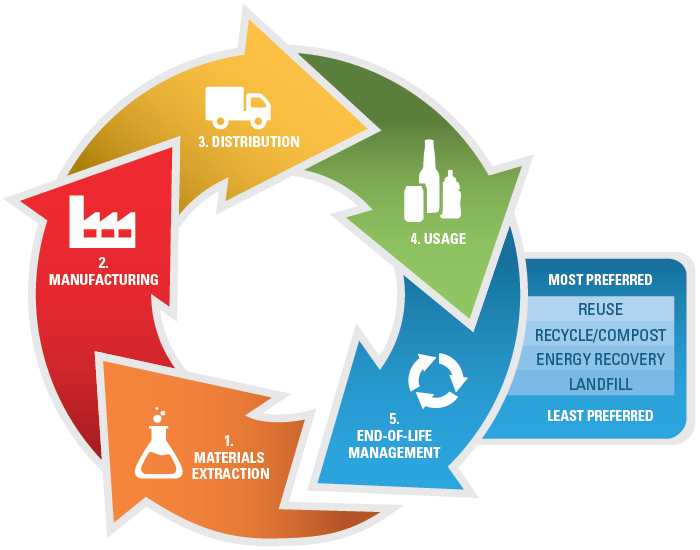
Constructing a tropical industrial home with eco-friendly materials presents a unique opportunity to blend striking design with environmental consciousness. By prioritizing locally sourced, durable materials like bamboo and recycled wood, and by carefully considering the thermal properties of building elements, we can significantly reduce the environmental footprint of these homes. The initial investment in sustainable materials often translates to long-term cost savings through reduced energy consumption and lower maintenance needs.
Ultimately, the creation of beautiful, sustainable tropical industrial homes represents a powerful fusion of style, functionality, and ecological responsibility, paving the way for a more sustainable future in architecture.
Helpful Answers
What are the common pests affecting eco-friendly materials in tropical climates?
Termites, wood-boring insects, and fungal growth are common concerns. Proper treatment and selection of pest-resistant materials are crucial.
How does humidity affect the lifespan of eco-friendly building materials?
High humidity can accelerate the degradation of some materials, especially wood and certain natural fibers. Proper ventilation and the use of moisture-resistant treatments are essential.
Are there any government regulations or building codes specific to eco-friendly construction in tropical regions?
Regulations vary by location. Research local building codes and incentives for sustainable construction practices. Some regions offer tax breaks or subsidies for using eco-friendly materials.
How can I ensure the structural integrity of a home built with eco-friendly materials?
Proper engineering and design are critical. Consult with structural engineers experienced in sustainable building practices to ensure the home meets all safety standards.
What are the potential downsides of using reclaimed materials?
Reclaimed materials may require more preparation and cleaning. They might also have imperfections or variations in size and color, which could affect the overall aesthetic.