The raw, utilitarian beauty of concrete floors has captivated homeowners seeking an industrial aesthetic. This transformative material, once relegated to warehouses and factories, now graces the interiors of stylish, modern homes. Its enduring appeal stems not only from its striking visual impact—a seamless expanse of polished grey, perhaps accented with subtle stains or metallic pigments—but also from its inherent durability and longevity.
Concrete’s resistance to wear and tear makes it a particularly practical choice for high-traffic areas, offering a cost-effective alternative to more delicate flooring options like hardwood or tile over the long term. This exploration delves into the design, installation, and practical considerations of incorporating concrete floors into an industrial home renovation, revealing the science behind its enduring popularity.
From the initial subfloor preparation, a crucial step influencing the final result, to the meticulous polishing and sealing processes that reveal the concrete’s inherent character, each stage presents unique challenges and rewards. Understanding the thermal properties of concrete, its sound transmission characteristics, and potential moisture issues is paramount for creating a comfortable and functional living space. This guide will equip you with the knowledge to navigate these complexities, ultimately transforming your home into a testament to both industrial chic and modern practicality.
The Appeal of Concrete Floors in Industrial Home Renovations
The raw, utilitarian aesthetic of polished concrete floors perfectly complements the industrial design style, characterized by exposed brick, metal accents, and high ceilings. This flooring choice offers a unique blend of modern sophistication and rustic charm, creating a space that feels both lived-in and elegantly minimalist. The inherent versatility of concrete allows for customization through staining, polishing, and the incorporation of integral color, enabling homeowners to tailor the floor’s appearance to their specific design vision.
Aesthetic Qualities of Polished Concrete Floors in Industrial Homes
Polished concrete floors bring a distinctive visual appeal to industrial-style homes. The smooth, reflective surface enhances the feeling of spaciousness, particularly in lofts or open-plan layouts. The subtle variations in color and texture inherent in concrete contribute to its unique character, offering a natural, organic look that contrasts beautifully with the often stark lines of industrial design elements.
Different polishing techniques can achieve various levels of sheen, from a matte finish to a high-gloss reflection, allowing for a range of aesthetic effects. Furthermore, the ability to incorporate pigments during the concrete pour allows for the creation of floors in a wide variety of colors, from classic greys to bolder hues like deep reds or even vibrant blues, further enhancing the design possibilities.
Durability and Longevity of Concrete Floors in High-Traffic Areas
Concrete’s exceptional durability makes it an ideal choice for high-traffic areas common in homes, particularly those with an open floor plan. Its compressive strength far surpasses that of many other flooring materials, making it highly resistant to cracking, chipping, and scratching. Unlike wood or tile, concrete is less susceptible to damage from heavy furniture or impacts from dropped objects.
Properly installed and sealed concrete floors can withstand significant wear and tear, maintaining their structural integrity and aesthetic appeal for decades, representing a long-term, cost-effective investment. The inherent resistance to moisture also makes it suitable for areas prone to spills or humidity.
Cost-Effectiveness of Concrete Floors Compared to Other Flooring Options
While the initial installation cost of concrete floors might seem higher than some alternatives like vinyl or laminate, the long-term cost-effectiveness becomes apparent. The superior durability translates to reduced maintenance and replacement costs over the lifespan of the floor. Unlike hardwood floors, which require sanding, refinishing, and potential repairs, or tile, which can crack or become loose, concrete requires minimal upkeep.
This long-term savings, coupled with the increased property value often associated with high-quality flooring, makes concrete a financially sound choice for a renovation project, especially considering its lasting resilience.
Maintenance Requirements Comparison of Concrete, Hardwood, and Tile Floors
The following table compares the maintenance requirements of concrete, hardwood, and tile floors:
Flooring Type | Cleaning | Repair/Refinishing | Lifespan |
---|---|---|---|
Concrete | Regular sweeping or vacuuming; occasional damp mopping | Minimal; sealing every few years | 50+ years |
Hardwood | Regular sweeping or vacuuming; occasional damp mopping; avoid excessive moisture | Sanding and refinishing every few years; repairs for scratches and dents | 20-30 years (depending on wear and maintenance) |
Tile | Regular sweeping or vacuuming; occasional damp mopping; grout cleaning | Grout repair; tile replacement for cracks or breakage | 20-30 years (depending on wear and maintenance) |
Design Considerations for Concrete Floors
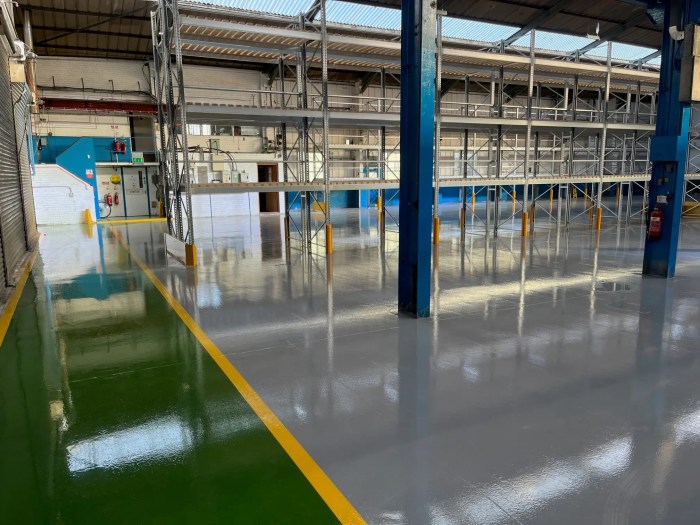
Concrete floors, a hallmark of industrial design, offer a unique blend of durability and aesthetic versatility. Their inherent strength and longevity make them ideal for high-traffic areas, while their adaptability to various finishes allows for seamless integration into a range of interior styles. Careful consideration of design elements, however, is crucial to achieving the desired industrial aesthetic and ensuring a harmonious flow within the space.
Concrete Finishes for Industrial Homes
The choice of concrete finish significantly impacts the overall look and feel of the space. Polished concrete, for instance, boasts a smooth, reflective surface that enhances the sense of spaciousness and modernity, often showcasing the aggregate’s inherent beauty. Stained concrete, on the other hand, allows for a wider spectrum of color customization, enabling designers to inject personality and depth into the floor.
The staining process penetrates the concrete’s pores, creating a rich, durable finish that resists wear and tear. Stamped concrete mimics the appearance of other materials like stone or brick, offering a textured alternative to the sleekness of polished concrete, adding a layer of visual interest while maintaining the durability of concrete. The selection depends on the desired level of sheen, color, and texture, aligning with the specific design vision for the industrial home.
The Impact of Color and Texture on Aesthetics
Color and texture are paramount in shaping the ambiance of an industrial-style home. Darker shades of concrete, such as charcoal grey or deep brown, create a dramatic and sophisticated atmosphere, often paired with exposed brick or metal accents to heighten the industrial feel. Lighter tones, such as light grey or even white, can offer a more airy and open feel, especially in smaller spaces.
The texture of the concrete itself contributes significantly to the overall aesthetic. A smooth, polished finish projects a clean, contemporary feel, whereas a textured, stamped surface can add a rustic or vintage touch, reflecting the raw, unfinished elements typical of industrial design. The interplay between color and texture creates a dynamic visual landscape that defines the character of the living space.
Concrete Flooring’s Integration with Industrial Design Elements
Concrete floors seamlessly integrate with other key elements of industrial design. The cool, neutral tones of concrete complement the warm, earthy tones of exposed brick walls, creating a balanced and visually appealing contrast. The clean lines of concrete flooring also work well with the metallic accents often found in industrial spaces, such as steel beams, pipes, or lighting fixtures.
This harmonious blend of materials reinforces the industrial theme, resulting in a cohesive and aesthetically pleasing interior. The raw, unfinished quality of concrete complements the exposed structural elements characteristic of industrial architecture, strengthening the overall design narrative.
Sample Floor Plan: Kitchen and Living Area
This sample floor plan illustrates the use of concrete floors in a kitchen and living area of an industrial-style home.
Area | Dimensions (ft) | Concrete Finish | Other Materials |
---|---|---|---|
Kitchen | 12 x 15 | Polished Concrete (medium grey) | Stainless steel appliances, dark wood cabinetry |
Living Area | 15 x 20 | Stained Concrete (dark brown) | Exposed brick wall, steel shelving unit |
The kitchen features polished medium grey concrete, providing a sleek, easy-to-clean surface that complements the stainless steel appliances and dark wood cabinetry. The adjacent living area utilizes stained dark brown concrete, creating a warm contrast to the exposed brick wall and the steel shelving unit, reflecting the raw aesthetic of industrial design. The seamless transition between the two areas emphasizes the unified design concept.
The overall effect is a sophisticated yet functional space that embraces the industrial style’s signature blend of functionality and aesthetic appeal.
Installation and Renovation Processes
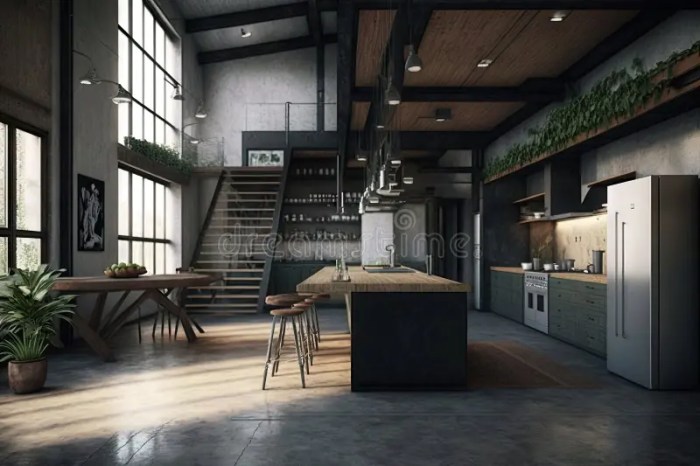
The transformation of a space using concrete floors involves a meticulous process, from subfloor preparation to achieving the desired polished finish. Understanding the intricacies of each stage ensures a durable and aesthetically pleasing result, minimizing potential problems and maximizing the lifespan of the flooring. This section details the key steps involved in both new installations and renovations of concrete floors.
Subfloor Preparation for Concrete Flooring Installation
Proper subfloor preparation is paramount for a successful concrete floor installation. A poorly prepared base can lead to cracking, settling, and an uneven surface. The process typically involves several key steps: First, the existing floor must be thoroughly cleaned to remove any debris, dust, or loose materials. This often involves sweeping, vacuuming, and potentially pressure washing, depending on the condition of the subfloor.
Next, any significant irregularities, such as large cracks or protrusions, need to be addressed. This might involve filling cracks with a suitable patching compound, grinding down high spots, or removing loose sections of the existing floor. Once the surface is clean and level, a moisture barrier is typically applied. This is crucial to prevent moisture from migrating up into the new concrete, causing damage.
Polyethylene sheeting is a common choice, overlapping seams and extending up the walls slightly. Finally, a vapor retarder is often applied over the moisture barrier to further prevent moisture vapor transmission. The final step involves installing a wire mesh reinforcement over the subfloor, which enhances the strength and durability of the concrete slab. This prevents cracking under stress and improves overall structural integrity.
Challenges Encountered During Concrete Floor Installation and Their Solutions
Several challenges can arise during concrete floor installation. One common issue is uneven settling. This can occur if the subfloor isn’t properly compacted or if the base is unstable. The solution involves using a self-leveling compound to create a perfectly flat surface before pouring the concrete. Another challenge is cracking, often caused by insufficient reinforcement or rapid drying.
Adding extra reinforcing mesh and using a concrete mix with appropriate water-cement ratio helps prevent this. Air pockets are another concern; they weaken the concrete and can lead to surface imperfections. Proper vibration during pouring helps to eliminate air pockets and ensures a dense, uniform slab. Finally, achieving the desired level of smoothness and flatness can be challenging.
This is often addressed through grinding and polishing after the concrete has cured.
Polishing and Sealing Concrete Floors
Polishing and sealing are crucial steps in achieving the desired aesthetic and durability of a concrete floor. The polishing process involves using progressively finer diamond grinding pads to remove imperfections and create a smooth, glossy surface. This multi-stage process typically starts with coarse pads to remove scratches and level the surface, followed by finer pads to create a progressively smoother and shinier finish.
The final polishing stage may use very fine pads or even polishing compounds to achieve a high-gloss sheen. After polishing, a sealant is applied to protect the concrete from stains, moisture damage, and wear. Penetrating sealers soak into the concrete, enhancing its durability and resistance to staining. Topical sealers create a protective film on the surface, offering additional protection against abrasion and spills.
The choice of sealer depends on the desired level of protection and the specific application.
Repairing Damaged Concrete Floors
Damaged concrete floors require careful repair to restore their structural integrity and aesthetic appeal. The repair process is dependent on the type and extent of damage.
- Crack Filling: Small cracks can be filled with epoxy or polyurethane-based crack fillers. These materials are designed to bond strongly with the concrete and resist cracking. The crack should be cleaned thoroughly before filling, ensuring complete adhesion.
- Surface Grinding: For larger cracks or uneven surfaces, surface grinding is often necessary. This involves using specialized grinding equipment to remove damaged concrete and create a level surface. Grinding can also remove stains or other surface imperfections.
- Patching: Significant damage, such as spalling or large holes, requires patching. This involves removing the damaged concrete and replacing it with a new concrete mix that matches the existing floor in color and texture. The patch should be carefully cured and then ground smooth to blend seamlessly with the surrounding area.
Addressing Practical Concerns
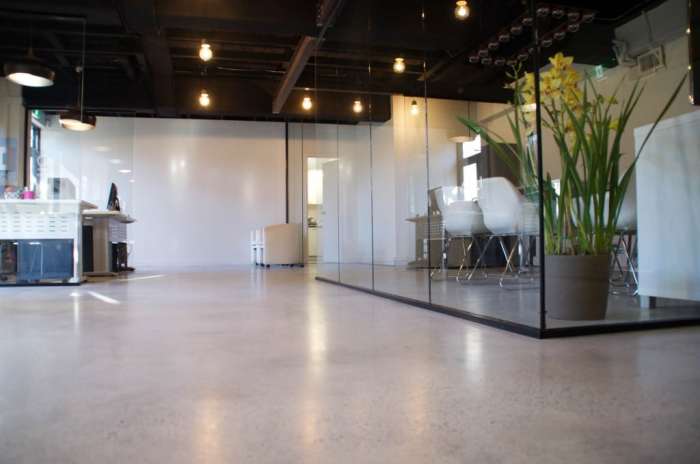
Concrete floors, while aesthetically pleasing and durable in industrial-style homes, present unique practical challenges. Understanding and addressing these concerns is crucial for creating a comfortable and functional living space. This section details the thermal, acoustic, and moisture-related properties of concrete and offers solutions for mitigating potential issues.
Thermal Properties and Temperature Fluctuation Mitigation
Concrete’s high thermal mass means it takes a long time to heat up and cool down. This can lead to uncomfortable temperature fluctuations, particularly in climates with significant seasonal variations. During summer, the floor can remain uncomfortably cool, while in winter, it can feel cold and drafty. Several strategies can mitigate this. Underfloor heating systems, either electric radiant mats or hydronic systems, provide effective and even heat distribution.
These systems are installed beneath the concrete slab before the final pour or, in some cases, on top of existing slabs. Alternatively, strategically placed area rugs can help insulate the floor and improve thermal comfort in specific areas. Thick, high-pile rugs made from wool or synthetic materials with good insulating properties are particularly effective. Finally, selecting appropriate window treatments can help regulate the indoor temperature, reducing the strain on the heating and cooling systems and minimizing the impact of external temperature changes on the concrete floor.
Sound Transmission Management
Concrete is a dense material, known for its excellent sound transmission properties. This means that noise from downstairs rooms, adjacent spaces, or even outside the building can easily travel through a concrete floor. To address this, a layered approach is typically employed. A resilient underlayment, such as a foam-based or rubber-based material, is installed between the concrete slab and the floor covering.
This creates a sound barrier, significantly reducing the transmission of impact noise (e.g., footsteps) and airborne noise (e.g., conversations). The thickness and density of the underlayment are crucial factors in its effectiveness. Additionally, selecting appropriate floor coverings such as carpet or rugs with thick padding can further enhance sound absorption. Carpet, in particular, is highly effective at absorbing sound waves, making it an excellent choice for rooms where sound reduction is a priority.
Moisture and Dampness Prevention
Concrete is a porous material and can absorb moisture from the ground or the surrounding environment. This moisture can lead to problems such as mold growth, efflorescence (salt deposits on the surface), and structural damage. Preventing moisture issues begins with proper installation. A vapor barrier should be installed beneath the concrete slab during construction to prevent moisture from rising from the ground.
This barrier should be a continuous, impermeable layer, properly sealed at all seams. Regularly inspecting the concrete for signs of moisture, such as dampness, discoloration, or musty odors, is also crucial. If moisture problems are detected, addressing the source of the moisture is essential. This might involve fixing leaks, improving drainage around the building, or installing a dehumidifier to control the humidity level in the home.
In severe cases, professional remediation may be required.
Underlayment and Rug Selection for Comfort and Acoustics
Choosing the right underlayment and rugs significantly impacts the comfort and acoustics of concrete floors. For underlayment, consider materials like foam rubber, cork, or recycled rubber. These materials offer varying degrees of cushioning and sound absorption. Thicker underlayments generally provide better insulation and sound dampening. The selection should consider the specific needs of the room.
For example, a high-density foam underlayment might be suitable for a bedroom, offering excellent sound insulation and comfort. In living areas, cork underlayment can provide both cushioning and a natural aesthetic. Regarding rugs, wool rugs offer superior insulation and sound absorption compared to synthetic materials. Thick-pile rugs are more effective at dampening sound and providing warmth underfoot.
However, the durability and maintenance requirements should also be considered. For high-traffic areas, a more durable, synthetic rug might be a better option. Consider the rug’s density, pile height, and fiber type when selecting the best option for the space.
Visual Examples and Inspirations
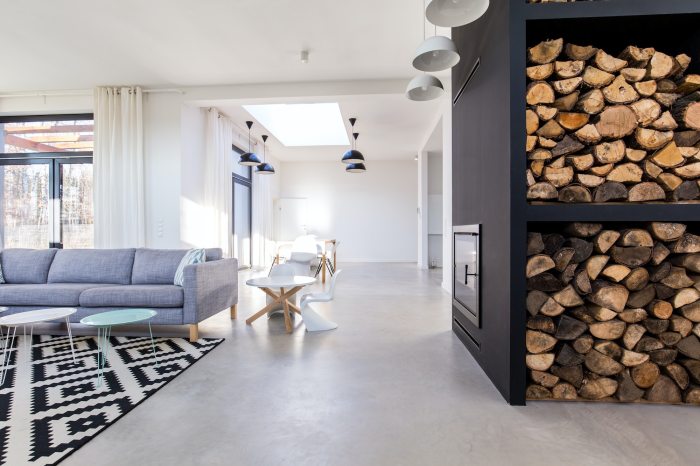
The visual impact of concrete floors in industrial-style homes is profoundly shaped by the interplay of surface treatment and color. The level of polish significantly affects the reflectivity and overall aesthetic, while staining introduces a spectrum of hues, enhancing the design’s character. Understanding these variables allows for the creation of unique and visually stunning spaces.Concrete’s inherent textural qualities are further emphasized by variations in polishing.
A highly polished concrete floor possesses a mirror-like sheen, reflecting light and creating a sense of spaciousness, often suitable for minimalist designs. Conversely, a lightly polished or honed finish retains a more natural, textured appearance, offering a rustic charm and visual warmth, better suited to spaces emphasizing raw industrial elements. Staining adds another layer of customization, allowing for the integration of specific color palettes to complement the overall interior design scheme.
Deep, rich browns evoke a sense of aged elegance, while cool grays create a modern and sophisticated atmosphere.
Concrete Floor Designs in Industrial Homes
This section details three distinct industrial-style home interiors, each showcasing the unique potential of concrete flooring. The variations in design elements, from the level of polish to the incorporation of other materials, highlight the adaptability of concrete in diverse settings.The first example features a spacious loft apartment with a highly polished, charcoal-gray stained concrete floor. The reflective surface amplifies the natural light streaming through large industrial-style windows, creating a bright and airy atmosphere.
Exposed brick walls and minimalist furniture further enhance the clean, modern aesthetic. The polished concrete floor acts as a neutral backdrop, allowing the other design elements to take center stage.The second example illustrates a more rustic industrial style. Here, the concrete floor is honed to a matte finish, revealing the natural aggregate and subtle textural variations. A warm, medium-brown stain complements the exposed wooden beams and reclaimed wood furniture, creating a cozy and inviting ambiance.
The slightly rougher texture of the floor adds to the overall sense of authenticity and warmth, contrasting with the smooth surfaces of other elements.The third example showcases a transitional industrial style, blending rustic elements with modern touches. The concrete floor is stained a deep, earthy tone, and features subtle metallic flecks throughout, adding visual interest and texture. This floor serves as a bridge between the exposed ductwork and raw brick walls, representing the industrial aspects of the design, and the sleek, modern furniture and lighting fixtures.
The interplay between the stained concrete and the other design choices creates a balanced and sophisticated aesthetic.
Transformation of a Space Before and After Concrete Floor Installation
Imagine a dilapidated warehouse space, its original wooden floorboards worn and uneven, the overall ambiance characterized by dust and decay. The walls are bare brick, showing signs of age and neglect. The lighting is dim and inadequate, emphasizing the space’s neglected state. This space feels cold, uninviting, and far from functional.After the installation of a polished, mid-grey stained concrete floor, the transformation is striking.
The new floor immediately elevates the space, creating a sense of order and modernity. The smooth, reflective surface amplifies the available light, making the space feel brighter and more open. The consistent color and texture of the concrete floor unify the space, providing a neutral backdrop that allows the other design elements – such as the exposed brick walls and newly installed lighting fixtures – to stand out.
The once cold and uninviting warehouse is now transformed into a sleek, contemporary living space. The improved lighting, coupled with the sleek concrete floor, creates a dramatic contrast with the space’s previous state, showcasing the transformative power of a carefully chosen concrete floor.
Last Point
Integrating concrete floors into an industrial home renovation offers a compelling blend of aesthetic appeal and practical functionality. The versatility of concrete, from its ability to accept various finishes and colors to its inherent durability, makes it a standout choice for homeowners seeking a unique and long-lasting flooring solution. By carefully considering design elements, addressing potential challenges during installation, and understanding the material’s thermal and acoustic properties, you can create a space that seamlessly merges industrial style with modern comfort.
The journey from initial concept to the finished, polished surface is a testament to the transformative power of design and the enduring appeal of concrete in the modern home.
Quick FAQs
Can concrete floors be heated?
Yes, radiant heating systems can be installed under concrete floors, providing efficient and even warmth. This is particularly beneficial in mitigating the naturally cool nature of concrete.
Are concrete floors susceptible to cracking?
While concrete is durable, cracking can occur due to settling or expansion/contraction. Proper subfloor preparation and the use of control joints during installation minimize this risk.
How do I clean concrete floors?
Regular sweeping or vacuuming removes loose debris. For deeper cleaning, use a pH-neutral cleaner and avoid harsh chemicals that could damage the sealant.
Can I install concrete floors over existing flooring?
Depending on the existing flooring’s condition and type, it might be possible. However, careful assessment and preparation are crucial to ensure a stable and level base.
What about the impact on allergies?
Sealed concrete floors are relatively easy to clean, reducing allergens compared to porous materials like carpet. However, regular cleaning remains essential.